Device for printing laser crystal cooling heat sinks and method thereof
A technology of laser crystals and heat sinks, which is applied to lasers, laser components, phonon exciters, etc., can solve problems such as poor contact, high processing costs, and poor heat dissipation and cooling effects, so as to improve heat dissipation effects, avoid pollution, Ensure consistent thickness
- Summary
- Abstract
- Description
- Claims
- Application Information
AI Technical Summary
Benefits of technology
Problems solved by technology
Method used
Image
Examples
Embodiment 1
[0035] Such as figure 1 As shown, a device for printing a laser crystal cooling heat sink includes a workbench 8, a laser crystal 1, a first clamp 21, a second clamp 22, a second support block 4, a first motor 3, a second motor 9, a laser 5. Powder feeder 6 and control module 7. The second support block 4, the first motor 3, the second motor 9 and the laser 5 are all fixedly connected to the surface of the workbench 8, the laser crystal 1 is cylindrical, and the first clamp 21 and the second clamp 22 are cylindrical, respectively against On both ends of the laser crystal 1, the area of the abutting surface of the first fixture 21 is larger than the area of the end surface of the laser crystal 1 abutting against it, and the area of the abutting surface of the second fixture 22 is larger than the area of the end surface of the laser crystal 1 abutting against it. The two faces of the fixture that are against the laser crystal completely cover the two end faces of the laser
Embodiment 2
[0044]When printing the cooling heat sink on the surface of the sheet-shaped laser crystal 1, the same part as the embodiment (1) will not be repeated, the difference is: the first motor 3 is not needed, and the third motor is fixedly connected to the laser 5 side. The three motors are connected to the control module 7, and the third motor drives the laser 5 to move in a plane perpendicular to the workbench 8. The sheet-shaped laser crystal 1 is placed perpendicular to the workbench 8, and the surface of the cooling heat sink 11 that needs to be printed faces the laser 5 . The laser beam 51 forms a "back" path on the surface of the laser crystal 1 .
PUM
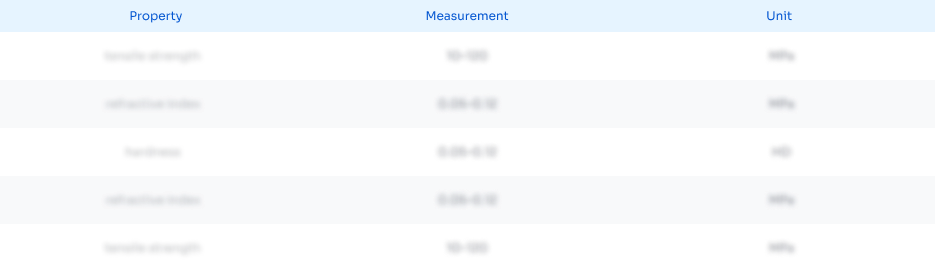
Abstract
Description
Claims
Application Information
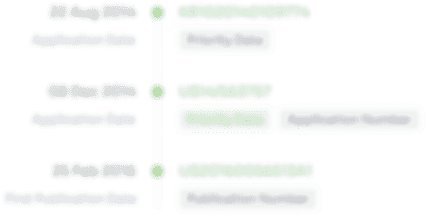
- R&D Engineer
- R&D Manager
- IP Professional
- Industry Leading Data Capabilities
- Powerful AI technology
- Patent DNA Extraction
Browse by: Latest US Patents, China's latest patents, Technical Efficacy Thesaurus, Application Domain, Technology Topic.
© 2024 PatSnap. All rights reserved.Legal|Privacy policy|Modern Slavery Act Transparency Statement|Sitemap