Method for connecting thermoplastic composite with metal
A technology of composite materials and connection methods, which is applied in the field of connection between carbon fiber thermoplastic composite materials and metals, can solve the problems of implanting electromagnetic sensitive materials, and achieve the effects of avoiding electromagnetic sensitive materials, fast connection speed and simple equipment
- Summary
- Abstract
- Description
- Claims
- Application Information
AI Technical Summary
Problems solved by technology
Method used
Examples
Example Embodiment
[0022] Example 1: Combination figure 1 and figure 2 Describe the embodiment, this embodiment is realized through the following steps:
[0023] Step 1. Use physical or chemical methods to roughen the to-be-welded surface of the metal piece, clean it up and dry it. For metal parts that are prone to electrochemical corrosion with carbon fiber composite materials, such as aluminum alloys, magnesium alloys, etc., measures such as anodizing or coating should be used to protect them. In the figure, workpiece 1 is a metal part, and workpiece 2 is a thermoplastic composite part. In such a tooling position, the skin depth of the induction magnetic field into the metal piece should preferably be smaller than the thickness of the metal piece, the induced current is concentrated on the upper surface of the workpiece 1, and the heat generated by the induction heating is also concentrated on this surface. Therefore, the heating rate of metal parts and the efficiency of induction heating are
Example Embodiment
[0031] Example 2: Combination figure 1 and image 3The embodiment is described. In this embodiment, the workpiece 2 is a thermoplastic composite material, and the workpiece 1 is a metal part. In such a tooling position, the skin depth of the magnetic field into the metal part should be preferably greater than the thickness of the metal part. At this time, the induced current is distributed in the entire workpiece 1, and the heat generated by induction heating is distributed in the metal part. Therefore, the heating speed of the metal parts and the efficiency of induction heating can be guaranteed. Other steps are identical with embodiment 1.
[0032] The workpiece 1 is close to the induction coil in this tooling position, and the distance between the induction coil and the workpiece 1 is not affected by other workpieces, so the heating efficiency of the induction magnetic field to the workpiece 1 is relatively high. However, since the heat generated by induction heating needs
Example Embodiment
[0033] Example 3:
[0034] A method for connecting a thermoplastic composite material to a metal, comprising the steps of:
[0035] Step 1. Roughen the surface of the metal part to be welded and the thermoplastic composite material part to be welded, clean and dry; the material of the metal part can be steel, aluminum alloy, magnesium alloy, titanium, nickel and other metals One of. For metal parts that are prone to electrochemical corrosion with reinforcing fibers, such as aluminum alloys, magnesium alloys and carbon fibers, etc., measures such as anodic oxidation or coating should be used to protect them;
[0036] The material of the thermoplastic composite material used should be fiber-reinforced thermoplastic resin composite material, and the material of thermoplastic composite material part should be fiber-reinforced thermoplastic resin composite material. The fiber-reinforced thermoplastic resin composite material consists of reinforcing fiber, matrix resin, auxiliary mate
PUM
Property | Measurement | Unit |
---|---|---|
Length | aaaaa | aaaaa |
Length | aaaaa | aaaaa |
Coil turns | aaaaa | aaaaa |
Abstract
Description
Claims
Application Information
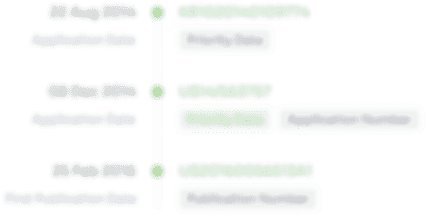
- R&D Engineer
- R&D Manager
- IP Professional
- Industry Leading Data Capabilities
- Powerful AI technology
- Patent DNA Extraction
Browse by: Latest US Patents, China's latest patents, Technical Efficacy Thesaurus, Application Domain, Technology Topic.
© 2024 PatSnap. All rights reserved.Legal|Privacy policy|Modern Slavery Act Transparency Statement|Sitemap