Parallel assembly method, device and equipment for complex optical-electro-mechanical system, and medium
An assembly method, opto-mechanical technology, applied in manufacturing computing systems, design optimization/simulation, resources, etc., can solve problems such as difficulty in meeting assembly efficiency and assembly performance, and achieve the effect of high-efficiency assembly and production.
- Summary
- Abstract
- Description
- Claims
- Application Information
AI Technical Summary
Benefits of technology
Problems solved by technology
Method used
Image
Examples
Embodiment Construction
[0042] The following will clearly and completely describe the technical solutions in the embodiments of the present invention with reference to the accompanying drawings in the embodiments of the present invention. Obviously, the described embodiments are only some, not all, embodiments of the present invention. Based on the embodiments of the present invention, all other embodiments obtained by persons of ordinary skill in the art without making creative efforts belong to the protection scope of the present invention.
[0043] The invention provides a parallel assembly method for complex opto-mechanical systems, such as figure 1 shown, including the following steps:
[0044] S101. Collect data on the assembly objects in the physical space, and improve the calculation model in the digital space according to the collected data;
[0045] In practical applications, the physical space corresponds to the actual assembly system, and the digital space corresponds to the virtual assembl
PUM
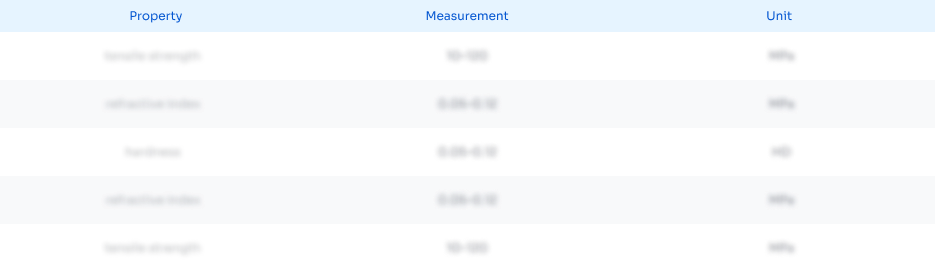
Abstract
Description
Claims
Application Information
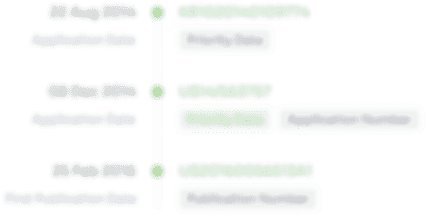
- R&D Engineer
- R&D Manager
- IP Professional
- Industry Leading Data Capabilities
- Powerful AI technology
- Patent DNA Extraction
Browse by: Latest US Patents, China's latest patents, Technical Efficacy Thesaurus, Application Domain, Technology Topic.
© 2024 PatSnap. All rights reserved.Legal|Privacy policy|Modern Slavery Act Transparency Statement|Sitemap