Device for detecting tool tip position of remote-controlled actuator
a technology of remote control actuator and device, which is applied in the direction of osteosynthesis devices, prosthesis, applications, etc., can solve the problems of difficult to accurately estimate the tip position, difficult to fit the marker directly to the tool, and elongated pipe sections, etc., to achieve good attitude stability and good attitude stability of the distal end member relative to the external for
- Summary
- Abstract
- Description
- Claims
- Application Information
AI Technical Summary
Benefits of technology
Problems solved by technology
Method used
Image
Examples
Embodiment Construction
[0088]A first preferred embodiment of a remote controlled actuator provided with a tool tip position detecting device designed in accordance with the present invention is shown in FIG. 1. This remote controlled actuator, generally identified by 5, includes a main body housing 4, a spindle guide 3 of an elongated shape having a base end connected with the main body housing 4, and a tool 1 rotatably supported by a tip end of the spindle guide 3. A tool rotation drive source 41 is provided within the main body housing 4 and a rotation of the tool rotation drive source 41 is transmitted to the tool 1 through a drive transmission unit 22 inserted within the spindle guide 3. The tool rotation drive source 41 may, however, be provided outside the main body housing 4. The main body housing 4 is provided with the operator unit 51 for performing a switching on and off of the tool rotation drive source 41 and an adjusting operation of the rotational speed.
[0089]The main body housing 4 is connecte
PUM
Property | Measurement | Unit |
---|---|---|
Flexibility | aaaaa | aaaaa |
Strain point | aaaaa | aaaaa |
Threshold limit | aaaaa | aaaaa |
Abstract
Description
Claims
Application Information
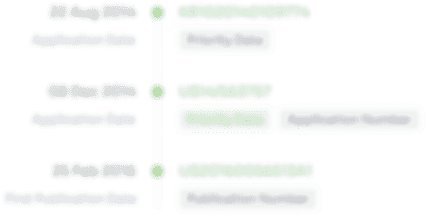
- R&D Engineer
- R&D Manager
- IP Professional
- Industry Leading Data Capabilities
- Powerful AI technology
- Patent DNA Extraction
Browse by: Latest US Patents, China's latest patents, Technical Efficacy Thesaurus, Application Domain, Technology Topic.
© 2024 PatSnap. All rights reserved.Legal|Privacy policy|Modern Slavery Act Transparency Statement|Sitemap