Fully balanced micro-machined inertial sensor
a micro-machined inertial sensor and fully balanced technology, applied in the direction of instruments, acceleration measurement using interia forces, devices using electric/magnetic means, etc., can solve the problem of adding material losses, causing load on the springs, and creating acoustic energy loss into the substra
- Summary
- Abstract
- Description
- Claims
- Application Information
AI Technical Summary
Benefits of technology
Problems solved by technology
Method used
Image
Examples
Embodiment Construction
[0088]The illustrated embodiments disclose a balanced Coriolis vibratory gyroscope architecture that is force and torque balanced on both x and y modes. In contrast to tuning fork Coriolis Vibratory Gyroscopes, which are torque balanced only on one axis, this architecture is torque balanced on both axes (modes). As a result anchor losses are minimized not only on one but on two axes, which helps achieve high Q-factor on both modes of the Coriolis Vibratory Gyroscope.
[0089]One implementation of such an architecture is a z-axis gyroscope 10 depicted in FIG. 1 where the gyroscope 10 is sensitive to rotation along the out-of-plane z axis. The gyroscope 10 is force and torque balanced as a result anchor losses are minimized not only one but two axes. Which helps achieve high Q-factor on both modes of the Coriolis Vibratory Gyroscope, diagrammatically depicted in FIG. 2. The gyroscopic mechanical element is comprised of two proof masses, a central tine 12 and a frame 14 around it. The frame
PUM
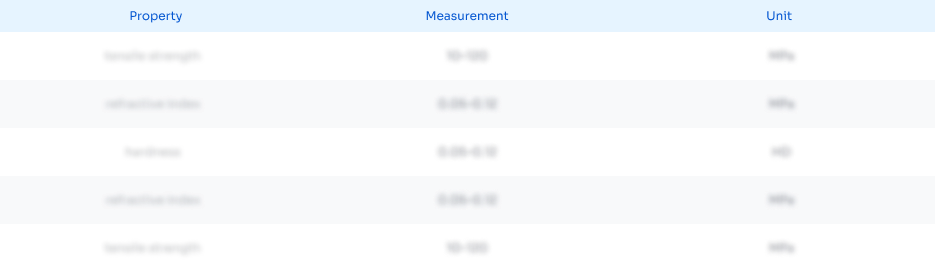
Abstract
Description
Claims
Application Information
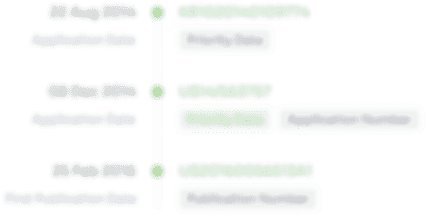
- R&D Engineer
- R&D Manager
- IP Professional
- Industry Leading Data Capabilities
- Powerful AI technology
- Patent DNA Extraction
Browse by: Latest US Patents, China's latest patents, Technical Efficacy Thesaurus, Application Domain, Technology Topic.
© 2024 PatSnap. All rights reserved.Legal|Privacy policy|Modern Slavery Act Transparency Statement|Sitemap