Array-type handling device and handling method
A pick-and-place device, array-type technology, applied in the field of array-type pick-and-place devices, can solve the problems of wasted time and travel, equipment wear and failure rate, low production efficiency, etc., to reduce the waste of time and distance, and reduce equipment wear and failure rate, and the effect of improving filling accuracy
- Summary
- Abstract
- Description
- Claims
- Application Information
AI Technical Summary
Problems solved by technology
Method used
Examples
Example Embodiment
[0088] Example 1
[0089] Reference figure 1 , 5 And the following table, the pick-and-place device is used to fill the base with four rows of A, B, C, D, eight columns of 1, 2, 3, 4, 5, 6, 7, and 8 arranged in four rows and eight columns. Take two loading substrates placed side by side as an example to illustrate the filling process of the pick and place device to fill the substrates. Among them, H is the spacing between two adjacent rows of the filling substrate along the Y-axis direction, and A is the spacing between two adjacent rows of the filling substrate along the X-axis direction.
[0090] In the embodiment of the array type pick-and-place device of the present invention, each filling head takes the object to be filled, fills in order, and fills all the objects on the filling head; takes the object to be filled, in order Fill... until the complete pick-and-place device is filled with the base. If the filling head is still filled with the substrate after filling the entire p
Example Embodiment
[0112] Example 2
[0113] The difference from Example 1 is that it is filled with a3, b3, c3, d3 first, then a2, b2, c2, d2, and finally a1, b1, c1, d1. The sequence of processing is the following steps:
[0114] 1. The pick-up position is located on the left side of the working platform, and the drive mechanism of the array pick-and-place device moves to the left from the safe position (the position is located on the right side of the working platform, within the travel range of the drive mechanism and does not interfere with other mechanical components) Move to the pickup position of the loaded object.
[0115] 2. 12 filling heads pick up the stuff to be filled,
[0116] 3. The driving mechanism moves the filling head a3, b3, c3, d3 to the right to above the filling position of A1, A3, A5, and A7,
[0117] 4. The four filling heads a3, b3, c3, and d3 simultaneously place the objects to be filled at the filling positions A1, A3, A5, and A7, filling four positions at a time, greatly impr
Example Embodiment
[0137] Example 3
[0138] Take the number of pick-and-place head assemblies 4, each pick-and-place head assembly is equipped with 3 filling heads, and a total of 12 filling heads are taken as an example. The processing method is a single piece, such as Image 6 As shown, the filling substrate array has 8 columns, and the number of rows is equal to the number of pick-and-place head components. The pickup position is located on the left side of the filling substrate. image 3 As shown, first fill with a1, b1, c1, d1, then fill with a2, b2, c2, d2, and finally fill with a3, b3, c3, d3 in the order of filling, the processing process is:
[0139] (1) The driving mechanism moves from the safe position to the visual calibration position, and the vision device calibrates the substrate to obtain the offset angle a, where a is the connection between the center of each column filling position and the Y axis of the movement mechanism or the filling position of each row The angle between the center
PUM
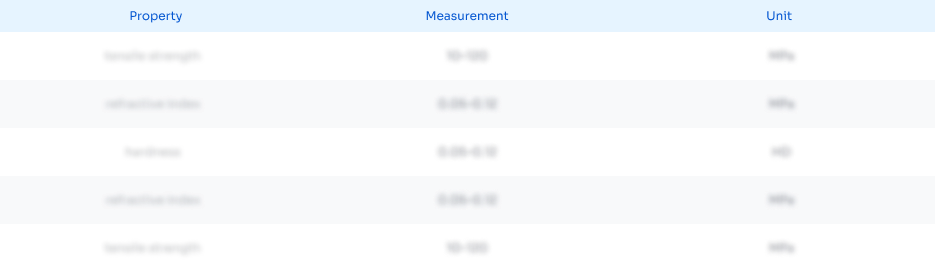
Abstract
Description
Claims
Application Information
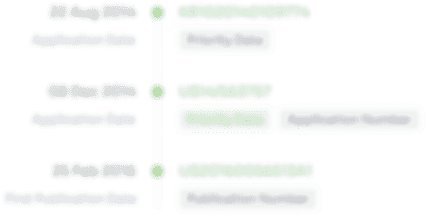
- R&D Engineer
- R&D Manager
- IP Professional
- Industry Leading Data Capabilities
- Powerful AI technology
- Patent DNA Extraction
Browse by: Latest US Patents, China's latest patents, Technical Efficacy Thesaurus, Application Domain, Technology Topic.
© 2024 PatSnap. All rights reserved.Legal|Privacy policy|Modern Slavery Act Transparency Statement|Sitemap