Multi-shaft mixed rapid control unit design method for micro assembly system
A technology of rapid control and unit design, applied in the direction of digital control, electrical program control, etc., can solve the problems of difficulty in secondary development, open internal control system, and high maintenance costs, to improve assembly efficiency, improve measurement accuracy, and improve positioning. The effect of precision
- Summary
- Abstract
- Description
- Claims
- Application Information
AI Technical Summary
Problems solved by technology
Method used
Image
Examples
Example Embodiment
[0020] The present invention will be described in further detail below in conjunction with the drawings:
[0021] figure 1 It is a system block diagram of a multi-axis hybrid rapid control unit for micro-assembly systems. The multi-axis hybrid rapid control unit for micro-assembly systems includes: TMS320F2812 chip, motor drivers 1 to 12, grating rulers 1, 2, photoelectric encoders 1, 2, Optocoupler isolation circuits 1 to 12, signal conditioning circuits 1, 2, quadruple frequency logic circuits 1, 2, stepping motors 1 to 12; among them, TMS320F2812 chip includes PWM output circuit, capture unit CAP, quadrature encoding circuit QEP and string Line port
[0022] Stepping motors 1 to 12 are connected to the PWM output circuit through motor drivers 1 to 12, respectively, stepping motors 1 to 12 are connected to serial ports through optocoupler isolation circuits 1 to 12, and stepping motors 1 to 12 are connected to micro The platform is connected, the grating scales 1, 2 are connected t
PUM
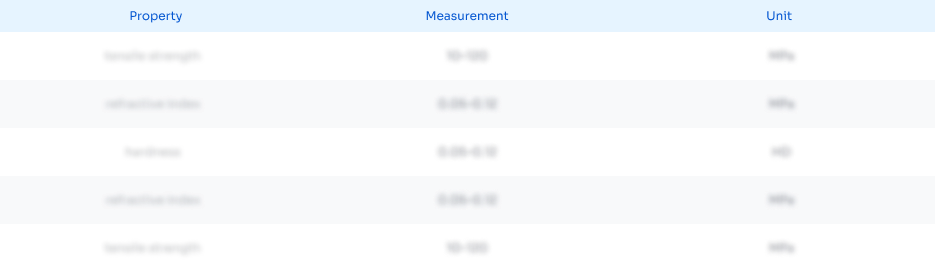
Abstract
Description
Claims
Application Information
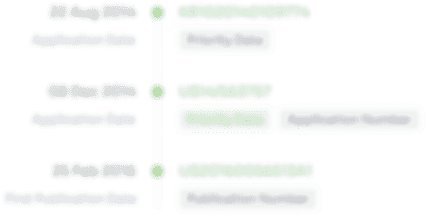
- R&D Engineer
- R&D Manager
- IP Professional
- Industry Leading Data Capabilities
- Powerful AI technology
- Patent DNA Extraction
Browse by: Latest US Patents, China's latest patents, Technical Efficacy Thesaurus, Application Domain, Technology Topic.
© 2024 PatSnap. All rights reserved.Legal|Privacy policy|Modern Slavery Act Transparency Statement|Sitemap