Core displacement control method and system
A technology of core displacement and control method, which is applied in the direction of earthwork drilling, measurement, wellbore/well components, etc., which can solve the problems of low automation and achieve the effect of convenient work and high control precision
- Summary
- Abstract
- Description
- Claims
- Application Information
AI Technical Summary
Benefits of technology
Problems solved by technology
Method used
Image
Examples
Embodiment 1
[0073] This embodiment one discloses a core displacement control method, refer to figure 1 , the method may include the following steps:
[0074] S101: Obtain in real time the parameter values of the monitoring parameters corresponding to the preset devices during the core displacement experiment.
[0075] S102: Based on a preset reference value, process the parameter value of the preset device monitoring parameter to obtain a processing result.
[0076] S103: Issue a corresponding control instruction according to the processing result, so as to realize the required control on the preset device.
[0077] When applying the present invention, specifically, the processing logic of each step of the present invention can be implemented on a computer in the form of a software system.
[0078] In order to realize the present invention, this embodiment set up a set of core displacement experimental device, refer to figure 2 , the device includes a computer 1 installed with the soft
Embodiment 2
[0094] In the second embodiment, refer to image 3 , the method may also include the following steps:
[0095] S104: Obtain the weight of the effluent from the core holder;
[0096] S105: regularly record the pressure value of each pressure measuring point detected by each pressure sensor according to the preset time interval;
[0097] S106: Process the pressure value of each pressure measuring point and the weight of the effluent, and calculate the resistance coefficient and residual resistance coefficient of the core on this basis.
[0098] Specifically, during the experiment, the effluent of the core holder is placed in the container on the balance at the outlet end, so that the balance can record the weight of the effluent, and the computer obtains the measurement data of the balance through the data acquisition system; and the computer obtains the measurement data of the balance through the set Recording mode, record the pressure value of each pressure measuring point at a
Embodiment 3
[0101] In this example, refer to Figure 5 , the method may also include the following steps:
[0102] S107: Obtain the real-time injection pressure of the injection pump. If the difference between the real-time injection pressure and the preset injection pressure exceeds a set value, the experiment is abnormal, and an abnormal alarm is issued.
[0103] In this embodiment, the computer obtains the injection pressure of the injection pump in real time through the data acquisition system. If the difference between the obtained real-time injection pressure and the set value of the injection pressure is within the specified range, the characterization experiment is normal; if the difference between the two is too large, then There is an abnormality in the characterization experiment. At this time, the technician needs to check the experimental device and troubleshoot the abnormality.
[0104] The software system of the present invention is provided with two control modes of remote c
PUM
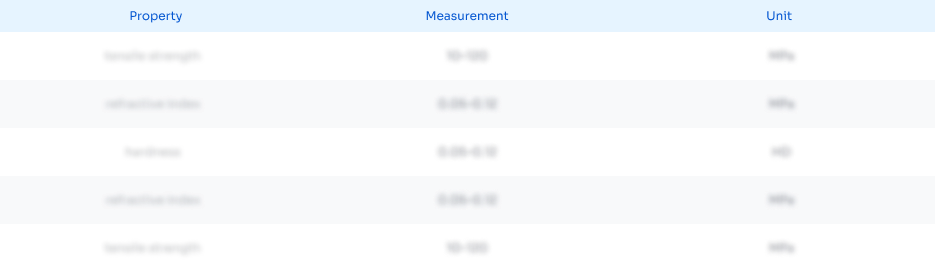
Abstract
Description
Claims
Application Information
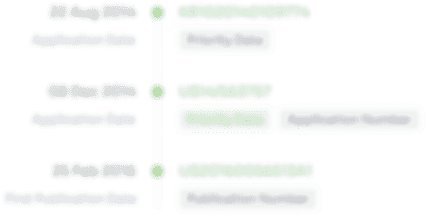
- R&D Engineer
- R&D Manager
- IP Professional
- Industry Leading Data Capabilities
- Powerful AI technology
- Patent DNA Extraction
Browse by: Latest US Patents, China's latest patents, Technical Efficacy Thesaurus, Application Domain, Technology Topic.
© 2024 PatSnap. All rights reserved.Legal|Privacy policy|Modern Slavery Act Transparency Statement|Sitemap