High-barrier composite membrane applied to thermal baffle
A technology of high-barrier composite film and heat insulation board, applied in the direction of synthetic resin layered products, flexible slender elements, flexible coverings, etc., can solve the problem of poor heat insulation performance of heat insulation film and heat insulation of heat insulation film Poor, affecting the normal use of the heat insulation board and other problems, to achieve good heat insulation performance and prevent ultraviolet radiation
- Summary
- Abstract
- Description
- Claims
- Application Information
AI Technical Summary
Benefits of technology
Problems solved by technology
Method used
Image
Examples
Embodiment 1
[0020] Such as figure 1 As shown, a high-barrier composite film applied to heat insulation boards of the present invention is formed by sequentially heat-sealing the first VMPET film layer 1, VMPET12 film layer 2, the second VMPET film layer 3, and PE heat-sealing layer 4, The first VMPET film layer 1 has a thickness of 10-14 microns, the VMPET12 film layer 2 has a thickness of 12 microns, the second VMPET film layer 3 has a thickness of 10-14 microns, and the PE heat-sealing layer 4 has a thickness of 40-80 microns. A polyurethane adhesive is provided between each adjacent layer.
[0021] In a further embodiment, the PET heat-sealing layer 4 , the first VMPET film layer 1 or the PE heat-sealing layer 4 are provided with laser anti-counterfeiting patterns.
[0022] In a further embodiment, the first VMPET film layer 1 has a thickness of 10 microns, the VMPET12 film layer 2 has a thickness of 12 microns, the second VMPET film layer 3 has a thickness of 10 microns, and the PE heat
PUM
Property | Measurement | Unit |
---|---|---|
Thickness | aaaaa | aaaaa |
Thickness | aaaaa | aaaaa |
Thickness | aaaaa | aaaaa |
Abstract
Description
Claims
Application Information
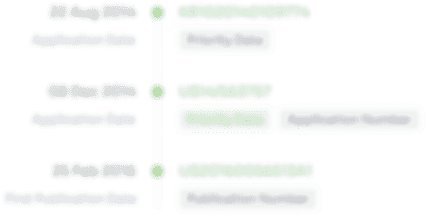
- R&D Engineer
- R&D Manager
- IP Professional
- Industry Leading Data Capabilities
- Powerful AI technology
- Patent DNA Extraction
Browse by: Latest US Patents, China's latest patents, Technical Efficacy Thesaurus, Application Domain, Technology Topic.
© 2024 PatSnap. All rights reserved.Legal|Privacy policy|Modern Slavery Act Transparency Statement|Sitemap