Piezoelectric windmill
A technology of electric windmills and piezoelectric vibrators, applied to electrical components, piezoelectric effect/electrostrictive or magnetostrictive motors, generators/motors, etc., can solve low reliability, poor wind speed adaptability, piezoelectric Problems such as two-way deformation of the vibrator achieve strong wind speed adaptability and high reliability
- Summary
- Abstract
- Description
- Claims
- Application Information
AI Technical Summary
Benefits of technology
Problems solved by technology
Method used
Image
Examples
Embodiment Construction
[0009] The end cover a is installed on the shell b through screws, and the buffer spring m is installed on the end cover a and the bottom wall b2 of the shell b through screws; The piezoelectric vibrator d and the excitation reed e are installed. The piezoelectric vibrator d is bonded by the substrate d1 and the piezoelectric sheet d2. The substrate d1 is installed close to the excitation reed e. The number of piezoelectric vibrators d on both sides of the excitation reed e Equal and symmetrical arrangement; the free end of the piezoelectric vibrator d is installed with a top block f via screws, and the top block f leans against the excitation reed e, and the free end of the excitation reed e is installed with a mass block h and an excited magnet through screws g; the left and right ends of the rotating shaft i are respectively installed on the end cover a and the bottom wall b2 of the housing b through the bearing j, and the two sections of the rotating shaft i are evenly install
PUM
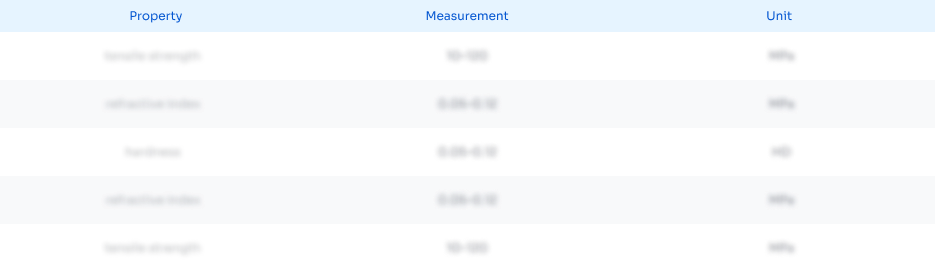
Abstract
Description
Claims
Application Information
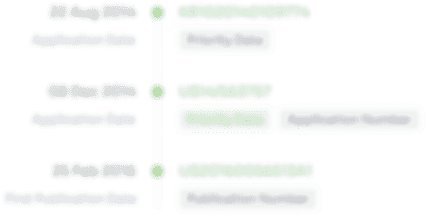
- R&D Engineer
- R&D Manager
- IP Professional
- Industry Leading Data Capabilities
- Powerful AI technology
- Patent DNA Extraction
Browse by: Latest US Patents, China's latest patents, Technical Efficacy Thesaurus, Application Domain, Technology Topic.
© 2024 PatSnap. All rights reserved.Legal|Privacy policy|Modern Slavery Act Transparency Statement|Sitemap