Plastic thermal riveted assembly monitoring method and device
A monitoring device and hot riveting technology, which is applied in the direction of measuring devices, optical device exploration, and material analysis, can solve problems such as high surface quality requirements, product welding defect assembly quality, unclear edges between targets and backgrounds, etc., to improve production efficiency and quality effects
- Summary
- Abstract
- Description
- Claims
- Application Information
AI Technical Summary
Problems solved by technology
Method used
Examples
Example Embodiment
[0018] The present invention will be further described below in conjunction with the accompanying drawings and implementation examples.
[0019] The plastic hot riveting assembly device includes a strong collimated light source module, a camera module, a system control module, and an auxiliary transportation and positioning module. It is used to form a specific shadow area for oblique riveting posts. In specific applications, multiple sets of strong collimated light source modules can be set according to needs. Different sets of strong collimated light source modules are arranged symmetrically in a ring; Appropriate object distance to photograph the welding column, where the object distance is determined by the selected lens and shooting resolution requirements; the system control module is used to control the light intensity and switch of the strong collimated light source, image acquisition cycle, auxiliary transport cycle, image analysis and Riveting quality judgment.
[0020
PUM
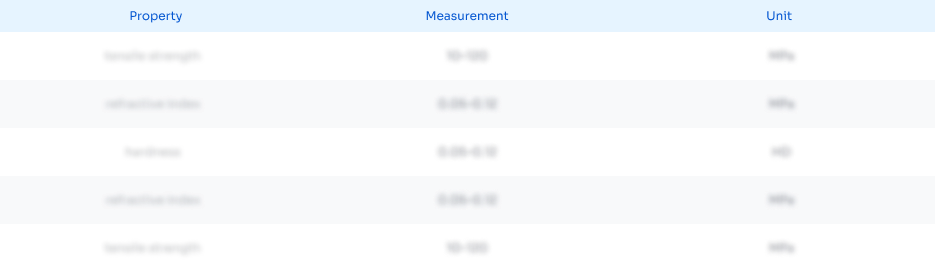
Abstract
Description
Claims
Application Information
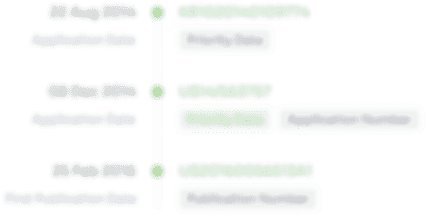
- R&D Engineer
- R&D Manager
- IP Professional
- Industry Leading Data Capabilities
- Powerful AI technology
- Patent DNA Extraction
Browse by: Latest US Patents, China's latest patents, Technical Efficacy Thesaurus, Application Domain, Technology Topic.
© 2024 PatSnap. All rights reserved.Legal|Privacy policy|Modern Slavery Act Transparency Statement|Sitemap