Method for confirming stress intensity factor distribution on member crack tip
A technology of stress intensity factor and crack front, applied in complex mathematical operations, etc., can solve problems such as low accuracy, low calculation efficiency, and poor mathematical simulation effect
- Summary
- Abstract
- Description
- Claims
- Application Information
AI Technical Summary
Problems solved by technology
Method used
Image
Examples
Embodiment 1
[0059] refer to figure 1 , figure 2 , image 3 , Figure 4 , Figure 5 , a method for determining the distribution of stress intensity factors at the crack front of structural parts, the method mainly includes the following steps (see attached figure 1 ):
[0060] (1) The basic equation of the general weight function method (variational integral equation) that gives the variational form of the problem to be solved, including thermal load, surface force load and body force load.
[0061] ∫ Γ 2 K I ( 1 ) K I ( 2 ) H δ c a ( s ) ds
Embodiment 2
[0089] refer to figure 1 , figure 2 , image 3 , Figure 4 , Figure 5 , Figure 6 , according to the method for determining the stress intensity factor distribution of the crack front of the structural member described in Example 1, the distribution of the stress intensity factor of the crack front of the semi-elliptical surface crack in the plate under thermal shock (thermal load) was determined. The figure below shows a semi-elliptical surface crack with a depth ratio of α / w=0.5 and a shape ratio of α / c=0.5, at Θ 0 = In the case of thermal shock at -300℃, the stress intensity factor distribution of the crack front changes with time. Among them, M is the dimensionless stress intensity factor, F o is the dimensionless time, φ is the position of the crack front (parameter angle), and Bi is the Biot number of the heat exchange condition at the time of impact. The distribution of the stress intensity factor along the crack front is determined for 60 time points in the f
Embodiment 3
[0092] refer to figure 1 , figure 2 , image 3 , Figure 4 , Figure 5 , Figure 7 , according to the method for determining the stress intensity factor distribution of the crack front of the structural member described in Example 1, the axial semi-elliptical surface crack in the circular tube acts simultaneously under the thermal shock (thermal load) and pressure shock (surface force load) (bearing The distribution of the stress intensity factor at the crack front under pressure-thermal shock) was determined. The figure below shows the axial semi-elliptical surface crack with a depth ratio of α / w=0.25 and a shape ratio of α / c=1 / 3, and the stress intensity factor distribution of the crack front changes with time under the pressure thermal shock of Rancho Seco process. Among them, K I is the stress intensity factor, t is the time, and φ is the position of the crack front (parameter angle). The stress intensity factor distribution of the crack front was determined fo
PUM
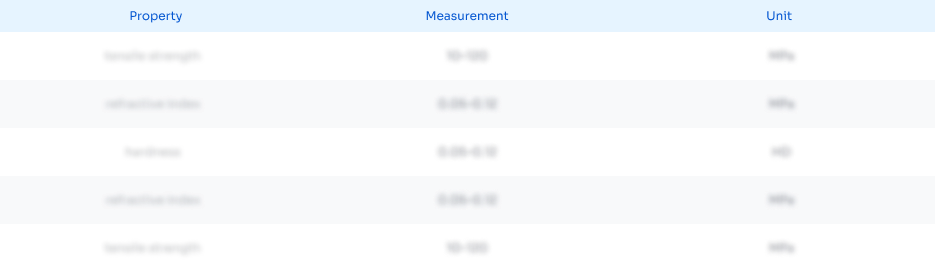
Abstract
Description
Claims
Application Information
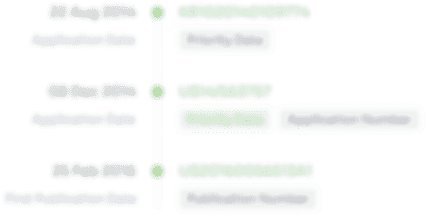
- R&D Engineer
- R&D Manager
- IP Professional
- Industry Leading Data Capabilities
- Powerful AI technology
- Patent DNA Extraction
Browse by: Latest US Patents, China's latest patents, Technical Efficacy Thesaurus, Application Domain, Technology Topic.
© 2024 PatSnap. All rights reserved.Legal|Privacy policy|Modern Slavery Act Transparency Statement|Sitemap