Coupling for compensating axle misalignment
- Summary
- Abstract
- Description
- Claims
- Application Information
AI Technical Summary
Benefits of technology
Problems solved by technology
Method used
Image
Examples
Example
[0013] Referring now to FIG. 1 there is illustrated a basic embodiment of a compensating coupling comprising a preferably monolithic mount, an outer ring 1 and an inner ring 2 interconnected by arcuate or curved webs 3a to 3d.
[0014] Referring now to FIG. 2 there is illustrated a modified embodiment of a compensating coupling which differs from the basic embodiment by points of force application 2′ being configured on the inner ring 2.
[0015] Referring now to FIG. 3 there is illustrated how the outer ring 1 of the compensating coupling is connected to a sheave 4 of a drive of which only part of a transmission ribbed belt 5 is indicated in FIG. 3. In FIG. 3 the inner ring 2 is connected for example to the wave generator 6 of a harmonic drive gearing.
[0016] It is because of the arcuate shape of the webs 3a to 3d that they are shortened or lengthened without being extended completely on application of a torque. The webs 3a to 3d are thus, because of the arcuate shape, subjected to substa
PUM
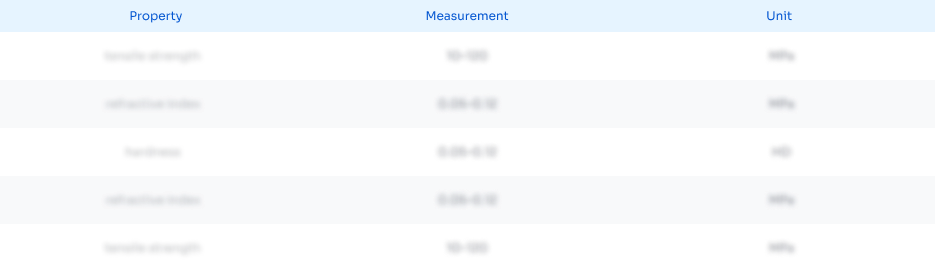
Abstract
Description
Claims
Application Information
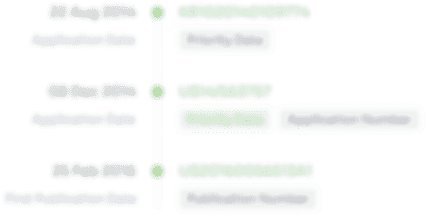
- R&D Engineer
- R&D Manager
- IP Professional
- Industry Leading Data Capabilities
- Powerful AI technology
- Patent DNA Extraction
Browse by: Latest US Patents, China's latest patents, Technical Efficacy Thesaurus, Application Domain, Technology Topic.
© 2024 PatSnap. All rights reserved.Legal|Privacy policy|Modern Slavery Act Transparency Statement|Sitemap