Eddy current mold level measuring device and mold level measuring method
a level measuring device and mold technology, applied in the direction of liquid/fluent solid measurement, volume measurement, instruments, etc., can solve the problems of inability to adapt, insufficient accuracy of above-described methods, and the inability to improve the accuracy of measuring devices, etc., to achieve the effect of ensuring the accuracy of the measurement devi
- Summary
- Abstract
- Description
- Claims
- Application Information
AI Technical Summary
Benefits of technology
Problems solved by technology
Method used
Image
Examples
Embodiment Construction
[0046]FIG. 1 shows an arrangement of continuous casting equipment.
[0047]Molten metal such as molten steel stored in a tundish 210 is poured into a mold 310 through an immersion nozzle 220, made to solidify in the mold 310 and delivered from the mold 310 through the use of pinch rolls 330. Further, the mold 310 is equipped with a mold oscillation device 320. Mold oscillation will be described later.
[0048]When in a certain time period an amount of molten metal which is poured into the mold 310 is greater than an amount of metal which is delivered from the mold 310, a level of a surface 400 of the molten metal in the mold 310 goes up. On the other hand, when in a certain time period an amount of metal which is delivered from the mold 310 is greater than an amount of molten metal which is poured into the mold 310, the level of the surface 400 of the molten metal in the mold 310 goes down. Under the above-described situation, an eddy current mold level measuring device according to an embod
PUM
Property | Measurement | Unit |
---|---|---|
Time | aaaaa | aaaaa |
Ratio | aaaaa | aaaaa |
Level | aaaaa | aaaaa |
Abstract
Description
Claims
Application Information
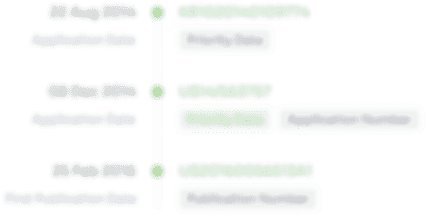
- R&D Engineer
- R&D Manager
- IP Professional
- Industry Leading Data Capabilities
- Powerful AI technology
- Patent DNA Extraction
Browse by: Latest US Patents, China's latest patents, Technical Efficacy Thesaurus, Application Domain, Technology Topic.
© 2024 PatSnap. All rights reserved.Legal|Privacy policy|Modern Slavery Act Transparency Statement|Sitemap