Method for improving product surface quality of hot rolling and leveling machine group
A technology of surface quality and smoothness, which is applied in the direction of workpiece surface treatment equipment, metal rolling, metal rolling, etc., can solve the problems of reducing the surface quality of finished products, large investment, and health damage to operators, so as to improve product surface quality and reduce Effect, the effect of a simple method
- Summary
- Abstract
- Description
- Claims
- Application Information
AI Technical Summary
Benefits of technology
Problems solved by technology
Method used
Image
Examples
Embodiment 1
[0017] Figure 1, figure 2 , image 3 As shown, the method for improving the product surface quality of the hot-rolled leveling unit is to carry out transverse bending (such as Figure 4 , Figure 5 As shown, the width direction of the strip is horizontal, and the length direction of the strip is vertical), peel off the iron oxide scale attached to the surface of the strip; then blow air on the surface of the strip on one side of the strip, and blow the peeled iron oxide towards On the other side of the steel, the peeled iron oxide scale is sucked away by the vacuum hood arranged on the other side of the strip.
[0018] Transverse bending is realized by scale removal device, which includes scale removal support 11, hydraulic cylinder 12, support frame 13, transverse bending pressure roller 14, the left end of support frame 13 is hinged with scale removal support 11, and the support frame The upper right end of 13 is hinged with the piston rod of the hydraulic cylinder 12, the c
Embodiment 2
[0021] It is basically the same as Embodiment 1, the difference is that: after the strip between the uncoiler 1 and the entrance turning pinch roller 3 is transversely bent, and before the strip surface is blown, the strip is longitudinally bent. bending (such as Image 6 , Figure 7 As shown), the iron oxide scale attached to the surface of the strip is peeled off.
[0022] Short longitudinal bending rollers 17 are arranged at both ends of the transverse direction (the width direction of the strip is the transverse direction) for the longitudinal bending of the strip, so that the longitudinal bending of the strip is carried out, and the oxide scale is further detached from the strip.
PUM
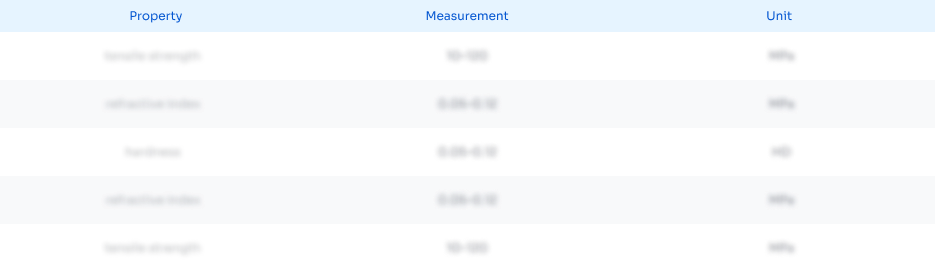
Abstract
Description
Claims
Application Information
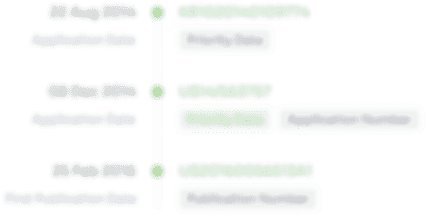
- R&D Engineer
- R&D Manager
- IP Professional
- Industry Leading Data Capabilities
- Powerful AI technology
- Patent DNA Extraction
Browse by: Latest US Patents, China's latest patents, Technical Efficacy Thesaurus, Application Domain, Technology Topic.
© 2024 PatSnap. All rights reserved.Legal|Privacy policy|Modern Slavery Act Transparency Statement|Sitemap