Vacuum induction melting method of high-oxygen-content steel
A technology of vacuum induction smelting and high oxygen content, applied in the field of vacuum induction smelting high oxygen content steel, can solve the problem of not being able to truly reflect the cutting performance of the design components, and achieve the effect of breaking through the technical bottleneck, speeding up the pace of development and improving the cutting performance.
- Summary
- Abstract
- Description
- Claims
- Application Information
AI Technical Summary
Problems solved by technology
Method used
Image
Examples
Embodiment 1
[0025] Low-carbon, high-sulfur, high-oxygen AISI 1215 free-cutting steel is smelted in a vacuum induction furnace with a charging capacity of 80kg.
[0026] 1. Chemical composition of the target steel grade: (unit: wt%)
[0027]
[0028] 2. Raw materials: (unit: wt%)
[0029]
[0030] 3. Specific operation steps:
[0031] 1) charging: put 78kg of industrial pure iron into the crucible;
[0032] 2) Vacuuming: After the vacuum degree is evacuated to 48Pa, it is filled with 5000Pa argon;
[0033] 3) Initial smelting: 78kg of industrial pure iron is induction smelted in the furnace until it is clear;
[0034] 4) Refining pre-decarburization: put 40g of iron oxide scale into the crucible, perform secondary vacuuming to make the vacuum degree reach 68Pa, and conduct induction refining for 8 minutes to remove a small amount of C, N and others in industrial pure iron Volatile impurity elements;
[0035] 5) Pre-oxygenation: After refining, fill the furnace with 5000Pa oxygen to
Embodiment 2
[0044] Low-carbon, high-sulfur, high-oxygen AISI 1215 free-cutting steel is smelted in a vacuum induction furnace with a charging capacity of 80kg.
[0045] 1. Chemical composition of the target steel grade: (unit: wt%)
[0046]
[0047] 2. Raw materials: (unit: wt%)
[0048] Same as Example 1.
[0049] 3. Specific operation steps:
[0050] 1) charging: put 78kg of industrial pure iron into the crucible;
[0051] 2) Vacuuming: After the vacuum degree is evacuated to 48Pa, it is filled with 5000Pa argon;
[0052] 3) Initial smelting: 78kg of industrial pure iron is induction smelted in the furnace until it is clear;
[0053] 4) Refining pre-decarburization: put 40g of iron oxide scale into the crucible, perform secondary vacuuming to make the vacuum degree reach 68Pa, and conduct induction refining for 8 minutes to remove a small amount of C, N and others in industrial pure iron Volatile impurity elements;
[0054] 5) Pre-oxygenation: After refining, fill the furnace with
PUM
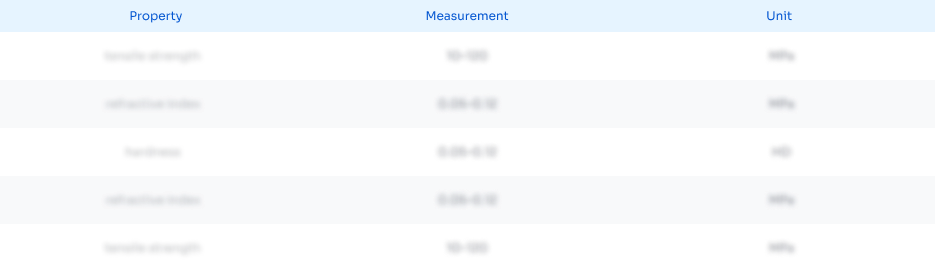
Abstract
Description
Claims
Application Information
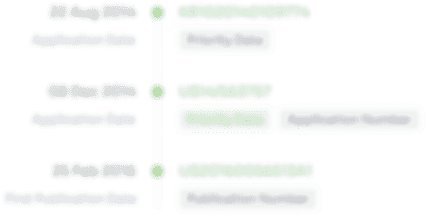
- R&D Engineer
- R&D Manager
- IP Professional
- Industry Leading Data Capabilities
- Powerful AI technology
- Patent DNA Extraction
Browse by: Latest US Patents, China's latest patents, Technical Efficacy Thesaurus, Application Domain, Technology Topic.
© 2024 PatSnap. All rights reserved.Legal|Privacy policy|Modern Slavery Act Transparency Statement|Sitemap