A Pre-straightening Method Realizing Shape Control of Medium and Heavy Plates
A shape control and pre-straightening technology, applied in the direction of contour control, metal rolling, manufacturing tools, etc., can solve problems such as buckling, achieve the effect of improving the shape, improving the pass rate of the shape and performance
- Summary
- Abstract
- Description
- Claims
- Application Information
AI Technical Summary
Problems solved by technology
Method used
Examples
Example Embodiment
[0015] Example 1
[0016] In this example, a piece of ASTM A283C steel plate is selected, the size of the blank is 150mm×2150mm×1121mm, the thickness of the intermediate billet is 24.04mm, the finishing rolling is 5 passes, the finishing rolling temperature is 986~990℃, and the finishing rolling temperature is 791~760℃. The target thickness of the steel plate is 5.9mm. The height of the exit side roll of the pre-straightening machine is 0mm.
[0017] 1) Before the ASTM A283C steel plate finish rolling, the first-level setting pre-straightening machine 7 roll gap mode is selected. After the first pass of finishing mill 1, the secondary system of finishing mill 1 sends ASTM A283C steel plate PDI data to the ultra-fast cooling secondary control system (steel ID number 1210591880, billet steel type Q235B, steel plate thickness 5.9mm, steel plate width 1660mm, Steel plate length 38950mm), the ultra-fast cooling secondary control system sends the data to the pre-straightening machine 7 co
Example Embodiment
[0021] Example 2
[0022] In this example, one piece of Q550D high-strength steel is selected, the size of the billet is 220mm×2220mm×1686mm, the thickness of the intermediate billet is 58.33mm, the finish rolling is 6 passes, the finish rolling temperature is 894~901℃, and the finish rolling temperature is 830~844℃. The target thickness of the steel plate is 25.1mm. The height of the exit side roll of the pre-straightening machine is -0.3mm.
[0023] 1) Prior to finishing rolling of Q550D high-strength steel, select the secondary setting pre-leveler 7 roll gap mode. After the first pass of finishing mill 1, the secondary system of finishing mill 1 sends Q550D high-strength steel PDI data to the ultra-fast cooling secondary control system (steel ID number 0810947834, billet steel type Q550D-2, steel plate thickness 25.1mm, steel plate width 2660mm, steel plate length 12970mm), the ultra-fast cooling secondary control system sends the data to the pre-straightening machine 7 control s
Example Embodiment
[0028] Example 3
[0029] In this example, a Q420BZ15 steel plate is selected, the size of the billet is 220mm×1840mm×2091mm, the thickness of the intermediate billet is 90.09mm, the finishing rolling is 6 passes, the finishing rolling temperature is 865~860℃, and the finishing rolling temperature is 848~860℃. The target thickness is 49.8mm. The height of the exit side roll of the pre-straightening machine is 0mm.
[0030] 1) Prior to finishing rolling of Q420BZ15 steel plate, select the secondary setting pre-leveler 7 roll gap mode. After the first pass of finishing mill 1, the secondary system of finishing mill 1 sends the Q420BZ15 steel plate PDI data to the ultra-fast cooling secondary control system (steel ID number 1230663741, blank steel type Q420-3, steel plate thickness 49.8mm, steel plate width 1940mm , Steel plate length 9240mm), the ultra-fast cooling secondary control system sends the data to the pre-straightening machine 7 control system, and the pre-straightening mach
PUM
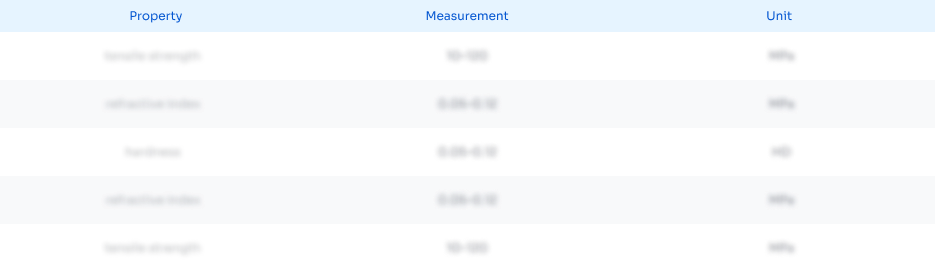
Abstract
Description
Claims
Application Information
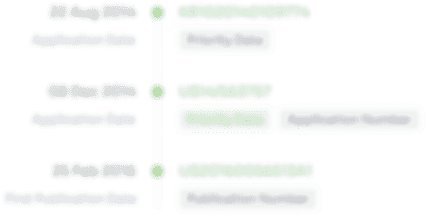
- R&D Engineer
- R&D Manager
- IP Professional
- Industry Leading Data Capabilities
- Powerful AI technology
- Patent DNA Extraction
Browse by: Latest US Patents, China's latest patents, Technical Efficacy Thesaurus, Application Domain, Technology Topic.
© 2024 PatSnap. All rights reserved.Legal|Privacy policy|Modern Slavery Act Transparency Statement|Sitemap