Double-fiber ball-shared coupling micro-measuring-force targeting sensor with end face micro-structure
A technology of aiming sensor and micro-measuring force, applied in measurement devices, instruments, optical devices, etc., can solve the problems of low primary magnification, low resolution, and reduced signal-to-noise ratio, so as to save costs and improve signal-to-noise ratio. The effect of improving the ratio and resolution
- Summary
- Abstract
- Description
- Claims
- Application Information
AI Technical Summary
Benefits of technology
Problems solved by technology
Method used
Image
Examples
Embodiment 1
[0028] A dual-fiber co-spherical coupling micro-measurement force aiming sensor with an end-face microstructure, the sensor consists of a laser 1, a beam expander collimator 2, a fiber coupling lens 3, a catheter 4, a probe 8, a microscope objective 10, CCD camera 11 and computer 12 constitute, and data line is communicated with CCD camera 11 and computer 12, and probe 8 is placed in the microhole 9 to be measured; The outgoing fiber 7 with a microstructure, the coupler 6 is respectively connected to the incident fiber 5 and the exiting fiber 7 with a tapered end surface microstructure, the coupler 6 is used as the contact point of the probe 8, and the beam emitted by the laser 1 is collimated by expanding the beam The mirror 2 and the fiber coupling lens 3 enter the incident fiber 5, the light beam is introduced into the coupler 6 through the incident fiber 5, and then is exported by the outgoing optical fiber 7 with a tapered end microstructure, and the exported light beam enter
Embodiment 2
[0033] The probe 8 is composed of an incident optical fiber 5, a coupler 6 and an outgoing optical fiber 13 with an aspherical end surface microstructure, and the aspherical end surface microstructure improves the signal-to-noise ratio of the detection signal. Other parts and working process of this embodiment are all the same as Embodiment 1.
Embodiment 3
[0035] The probe 8 is composed of an incident optical fiber 5, a coupler 6 and an outgoing optical fiber 14 with a spherical end surface microstructure, and the spherical end surface microstructure improves the signal-to-noise ratio of the detection signal. Other parts and working process of this embodiment are all the same as Embodiment 1.
PUM
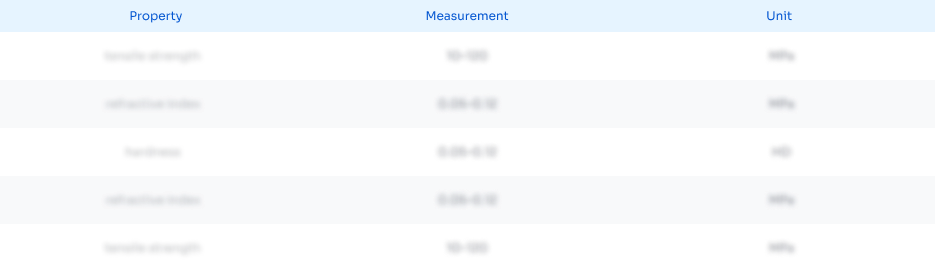
Abstract
Description
Claims
Application Information
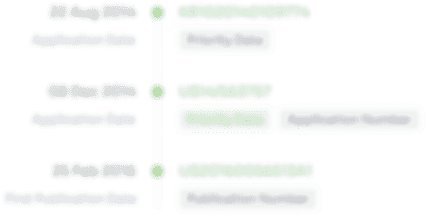
- R&D Engineer
- R&D Manager
- IP Professional
- Industry Leading Data Capabilities
- Powerful AI technology
- Patent DNA Extraction
Browse by: Latest US Patents, China's latest patents, Technical Efficacy Thesaurus, Application Domain, Technology Topic.
© 2024 PatSnap. All rights reserved.Legal|Privacy policy|Modern Slavery Act Transparency Statement|Sitemap