Online weighing roller way
A roller table and weighing technology, applied in the directions of weighing, measuring devices, instruments, etc., can solve the problems of high reconstruction cost and increase the civil foundation, and achieve the effect of low installation and reconstruction cost and easy installation.
- Summary
- Abstract
- Description
- Claims
- Application Information
AI Technical Summary
Benefits of technology
Problems solved by technology
Method used
Image
Examples
Embodiment 1
[0026] Such as figure 2 As shown, based on the above content, specifically, a pair of shear force sensors 12 are provided, and no support column 6 is provided in the measurement area. That is to say, the measurement area is set between two adjacent supporting columns 6, so that only a pair of shear force sensors 12 are needed to realize weighing detection.
[0027] Since the shear force sensor 12 is directly installed on the original conveying roller table 4, there is no need to cut off the conveying roller table 4, no need to modify the conveying roller table 4 during installation, no need to increase the civil foundation, no hydraulic system, and low weighing cost.
[0028] When weighing, after the workpiece 5 to be weighed is completely moved into the measuring area, the roller 2 stops rotating, the workpiece 5 no longer moves, and the shear force sensor 12 detects a parameter change, and the weight corresponding to the change is the weight of the workpiece 5. When the workp
Embodiment 2
[0030] Such as image 3 As shown, this embodiment is basically the same as Embodiment 1, the difference is that there are support columns 6 for supporting the conveying roller table 4 in the measurement area, and at least one support column 6 is provided on both sides of each support column 6 For the shear force sensors 12 , at least one pair of shear force sensors 12 is provided between two adjacent support columns 6 .
[0031] image 3 Shown is a schematic diagram of only one support column 6 in the measurement area, so that the influence of the support column 6 on the weighing result can be eliminated, and the true value of the workpiece 5 weight can be obtained after comprehensive processing of the detection results of many pairs of shear sensors 12, and the measurement The result is not affected, and workpieces with longer lengths can be measured 5 .
Embodiment 3
[0033] Such as Figure 4 As shown, this embodiment is basically the same as Embodiment 1, the difference is that a support column 6 is provided in the measurement area, and a pressure sensor 11 is connected to the support column 6 . Specifically, the pressure sensor 11 is arranged at the bottom of the support column 6 .
PUM
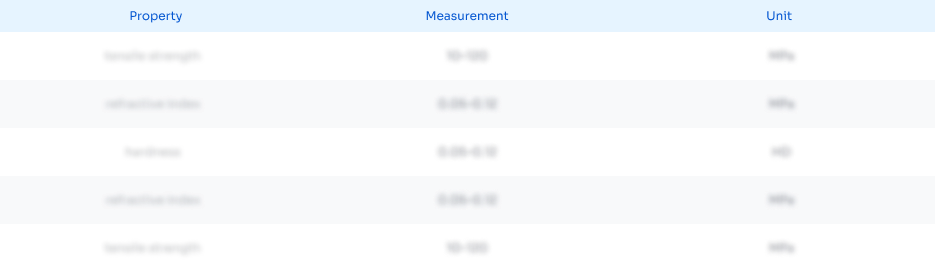
Abstract
Description
Claims
Application Information
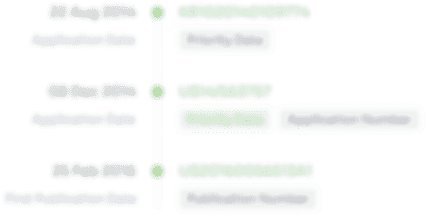
- R&D Engineer
- R&D Manager
- IP Professional
- Industry Leading Data Capabilities
- Powerful AI technology
- Patent DNA Extraction
Browse by: Latest US Patents, China's latest patents, Technical Efficacy Thesaurus, Application Domain, Technology Topic.
© 2024 PatSnap. All rights reserved.Legal|Privacy policy|Modern Slavery Act Transparency Statement|Sitemap