Dismounting-and-washing-free descaling method for dilute acid plate heat exchanger
A plate heat exchanger, no dismantling and cleaning technology, applied in the field of heat exchange, can solve the problems of reducing the service life of equipment, and achieve the effect of ensuring heat exchange efficiency, short time consumption, and avoiding damage
- Summary
- Abstract
- Description
- Claims
- Application Information
AI Technical Summary
Benefits of technology
Problems solved by technology
Method used
Image
Examples
Embodiment 1
[0015] Normal operation of dilute acid plate heat exchanger (such as figure 1 ) After every two months, carry out the following exchange: exchange the hot dilute sulfuric acid inlet 3 of the dilute acid plate heat exchanger with the cold cycle process water inlet 1, and at the same time reverse the hot dilute sulfuric acid outlet 4 with the cold cycle process water outlet 2, so that the original The flow channel leading to the hot dilute sulfuric acid is passed into the cold cycle process water, so that the flow path that was originally connected to the cold cycle process water is passed into the hot dilute sulfuric acid. The import and export of circulating process water are reversed and restored to the original state.
[0016] Further, the following branch pipes are made on each input pipeline to facilitate replacement: branch pipes are set on the main input pipe of hot dilute sulfuric acid, valves are set on both the main pipe and the branch pipe, the main pipe is connected wi
PUM
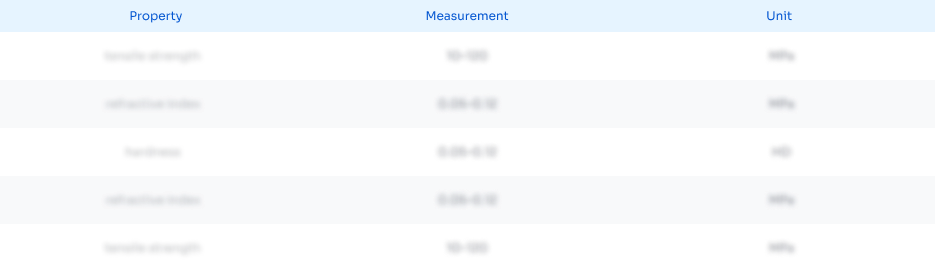
Abstract
Description
Claims
Application Information
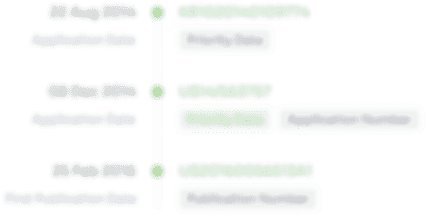
- R&D Engineer
- R&D Manager
- IP Professional
- Industry Leading Data Capabilities
- Powerful AI technology
- Patent DNA Extraction
Browse by: Latest US Patents, China's latest patents, Technical Efficacy Thesaurus, Application Domain, Technology Topic.
© 2024 PatSnap. All rights reserved.Legal|Privacy policy|Modern Slavery Act Transparency Statement|Sitemap