Thick ore body mining method
A technology for thick and large ore bodies and mining methods, applied in surface mining, mining equipment, underground mining, etc., can solve problems such as low work efficiency and potential safety hazards, and achieve the effect of improving work efficiency, preventing fragmentation and ensuring construction safety.
- Summary
- Abstract
- Description
- Claims
- Application Information
AI Technical Summary
Benefits of technology
Problems solved by technology
Method used
Image
Examples
Embodiment Construction
[0015] In the 401-2 panel area in the northwest of the Shanshuya mining area, the thickness of the ore seam is more than 8m, and the inclination angle of the ore seam is 3-5°. The structure of the roof near this area is poor, and the surface subsidence is not allowed in the later stage, so layered and segmented filling methods are adopted for mining. This technology adopts the step-by-step full-layer bottom-down mining technology to mainly solve the problem of secondary bottom-down in the process of stratification and segmentation, and at the same time improve the construction safety factor and effectively protect the lives and properties of operators. Aiming at the medium-thick phosphate ore body in the 401-2 panel (the average mining height is 8m), Shanshuya Mine researched and applied the box-type filling mining technology in the process of mining the ore in this panel, and along the cutting direction, the mines were separated on both sides of the mine house. The upper and low
PUM
Property | Measurement | Unit |
---|---|---|
Average height | aaaaa | aaaaa |
Particle size | aaaaa | aaaaa |
Abstract
Description
Claims
Application Information
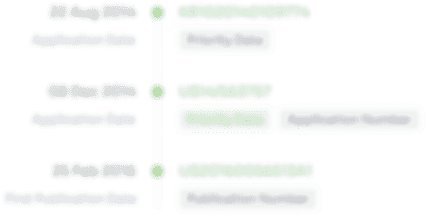
- R&D Engineer
- R&D Manager
- IP Professional
- Industry Leading Data Capabilities
- Powerful AI technology
- Patent DNA Extraction
Browse by: Latest US Patents, China's latest patents, Technical Efficacy Thesaurus, Application Domain, Technology Topic.
© 2024 PatSnap. All rights reserved.Legal|Privacy policy|Modern Slavery Act Transparency Statement|Sitemap