Preparation method of carbon cloth load nickel oxide coated iron oxide nanorod composite material
An iron oxide nanometer and composite material technology, applied in the manufacture of hybrid/electric double layer capacitors, hybrid capacitor electrodes, etc., can solve the problems of hindered ion diffusion, poor oxide binding, large contact resistance, etc., and achieve high crystallinity. Low requirements, good binding effect
- Summary
- Abstract
- Description
- Claims
- Application Information
AI Technical Summary
Problems solved by technology
Method used
Image
Examples
Embodiment 1
[0031] First, the purchased carbon cloth was sonicated with 32% concentrated nitric acid, ethanol, and deionized water for 30 minutes respectively.
[0032] 0.65gFeCl 3 (0.05M) and 0.57gNa 2 SO 4 (0.05M) was added to 40ml deionized water, then stirred at room temperature for 30min, the prepared solution was poured into a 50ml polytetrafluoroethylene-lined reactor, and then the treated carbon cloth (such as figure 1 ) into the reaction kettle, keep warm at 120°C for 8h, take it out after cooling, rinse repeatedly with deionized water, dry overnight at 60°C, and obtain iron oxide nanorod precursors with a diameter of 60-70nm and a length of 400-500nm . Weigh 2.38g of Ni(NO 3 ) 2 ·6H 2Add O (0.4M) and 0.3g urea (0.25M) to 20ml deionized water and stir at room temperature for 30min, pour it into a 50ml polytetrafluoroethylene-lined reactor, and then put the precursor into the reactor , kept at 90°C for 9h, rinsed repeatedly with deionized water after cooling, and dried overnig
Embodiment 2
[0034] First, the purchased carbon cloth was sonicated with 32% concentrated nitric acid, ethanol, and deionized water for 30 minutes respectively.
[0035] 0.65gFeCl 3 (0.05M) and 0.57gNa 2 SO 4 (0.05M) was added to 40ml deionized water, then stirred at room temperature for 30min, poured the prepared solution into a 50ml polytetrafluoroethylene-lined reactor, and then put the treated carbon cloth into the reactor. Insulate at 120°C for 8 hours, take it out after cooling, rinse repeatedly with deionized water, and dry overnight at 60°C to obtain iron oxide nanorod precursors with a diameter of 60-70nm and a length of 400-500nm. Weigh 2.38g of Ni(NO 3 ) 2 ·6H 2 Add O (0.4M) and 0.3g urea (0.25M) to 20ml deionized water and stir at room temperature for 30min, pour it into a 50ml polytetrafluoroethylene-lined reactor, and then put the precursor into the reactor , kept at 90°C for 6h, rinsed repeatedly with deionized water after cooling, and dried overnight at 60°C to obtain a
Embodiment 3
[0037] First, the purchased carbon cloth was sonicated with 32% concentrated nitric acid, ethanol, and deionized water for 60 minutes respectively.
[0038] 1.3gFeCl 3 (0.1M) and 1.14gNa 2 SO 4 (0.1M) was added to 40ml deionized water, then stirred at room temperature for 30min, poured the prepared solution into a 50ml polytetrafluoroethylene-lined reactor, and then put the treated carbon cloth into the reactor. Insulate at 100°C for 6h, take it out after cooling, rinse repeatedly with deionized water, and dry overnight at 60°C to obtain iron oxide nanorod precursors with a diameter of 70-80nm and a length of 500-600nm. Weigh 1.16g of Ni(NO 3 ) 2 ·6H 2 Add O (0.2M) and 0.6g (0.5M) urea to 20ml deionized water and stir at room temperature for 30min, pour it into a 50ml Teflon-lined reactor, and then put the precursor into the reactor , kept at 80°C for 18h, rinsed repeatedly with deionized water after cooling, and dried overnight at 60°C to obtain a nickel oxide iron oxide h
PUM
Property | Measurement | Unit |
---|---|---|
Diameter | aaaaa | aaaaa |
Length | aaaaa | aaaaa |
Thickness | aaaaa | aaaaa |
Abstract
Description
Claims
Application Information
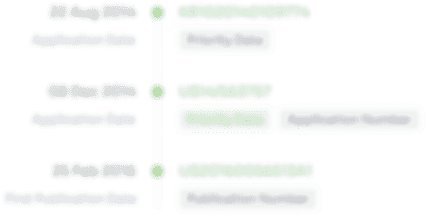
- R&D Engineer
- R&D Manager
- IP Professional
- Industry Leading Data Capabilities
- Powerful AI technology
- Patent DNA Extraction
Browse by: Latest US Patents, China's latest patents, Technical Efficacy Thesaurus, Application Domain, Technology Topic.
© 2024 PatSnap. All rights reserved.Legal|Privacy policy|Modern Slavery Act Transparency Statement|Sitemap