Polyurea metal salt composite bearing lubricating grease composition and preparation method thereof
A grease composition and composite bearing technology, applied in the field of grease, can solve the problem of weak extreme pressure and anti-wear performance, and achieve the effects of outstanding high temperature performance, improved extreme pressure and anti-wear performance, and long lubrication cycle
- Summary
- Abstract
- Description
- Claims
- Application Information
AI Technical Summary
Problems solved by technology
Method used
Examples
Example Embodiment
[0030] Example 1 First add 54 g of diisocyanate in the thickening agent to 445 g of autoclave oil. The autoclave oil is mineral oil. Add 40 g of organic amine to another part of 431 g of autoclave oil. The two reactors are heated to 60°C. , Put the two tanks of materials into the reaction kettle after 10 minutes of constant temperature, stir and heat to 75-80℃, react for 1~1.5h to produce diurea metal salt thickener without fiber crystal structure, and then proceed to diurea metal salt thickening Add 10g of barium dinonylnaphthalenesulfonate, control the temperature at 90~100℃, control the reaction time at 1~2h, slowly increase the temperature to the highest refining temperature of 180℃ to produce the dipolyurea with interlaced tubular fiber structure. Metal salt thickener, control the heating time between 1.5h and 2h, add 10g of antioxidant aromatic amine alkylated diphenylamine when the temperature is raised to 160℃-170℃; after the material is naturally cooled to below 80℃, Add
Example Embodiment
[0031] Example 2 First add 91g of the diisocyanate in the thickening agent to 411g of autoclave oil. The autoclave oil is mineral oil. Add 53g of organic amine to another part of 410g of autoclave oil. The two reactors are heated to 60°C. , Put the two tanks of materials into the reaction kettle after 10 minutes of constant temperature, stir and heat to 75-80℃, react for 1~1.5h to produce diurea metal salt thickener without fiber crystal structure, and then proceed to diurea metal salt thickening Add 10g of barium dinonylnaphthalenesulfonate, control the temperature at 90~100℃, control the reaction time at 1~2h, slowly increase the temperature to the highest refining temperature of 180℃ to produce the dipolyurea with interlaced tubular fiber structure. Metal salt thickener, control the heating time between 1.5h and 2h, during the heating to 160℃-170℃, add 5g of antioxidant aromatic amine alkylated diphenylamine, 2,6-di-tert-butyl- 10g of p-cresol. After the material is naturally
Example Embodiment
[0032] Example 3 First add 54 g of diisocyanate in the thickening agent to 445 g of autoclave oil. The autoclave oil is mineral oil. Add 40 g of organic amine to another part of 431 g of autoclave oil. The two reactors are heated to 60°C. , Put the two tanks of materials into the reaction kettle after 10 minutes of constant temperature, stir and heat to 75-80℃, react for 1~1.5h to produce diurea metal salt thickener without fiber crystal structure, and then proceed to diurea metal salt thickening Add 10g of sodium dinonylnaphthalene sulfonate, control the temperature at 90~100℃, control the reaction time at 1~2h, and slowly raise the temperature to the highest refining temperature 180℃ to produce the dipolyurea with interlaced tubular fiber structure. Metal salt thickener, control the heating time between 1.5h and 2h, add 10g of antioxidant aromatic amine alkylated diphenylamine when the temperature is raised to 160℃-170℃. After the material is naturally cooled to below 80°C, add
PUM
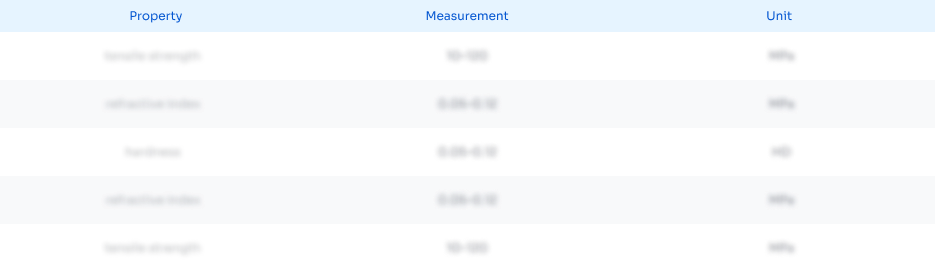
Abstract
Description
Claims
Application Information
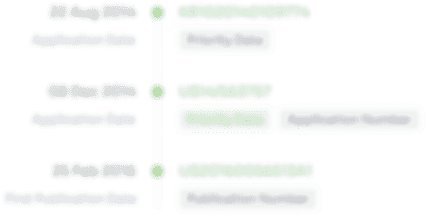
- R&D Engineer
- R&D Manager
- IP Professional
- Industry Leading Data Capabilities
- Powerful AI technology
- Patent DNA Extraction
Browse by: Latest US Patents, China's latest patents, Technical Efficacy Thesaurus, Application Domain, Technology Topic.
© 2024 PatSnap. All rights reserved.Legal|Privacy policy|Modern Slavery Act Transparency Statement|Sitemap