Preparation method of ion-modified titanium dioxide ceramic material with high dielectric constant and low dielectric loss
- Summary
- Abstract
- Description
- Claims
- Application Information
AI Technical Summary
Problems solved by technology
Method used
Image
Examples
Example Embodiment
[0015] Example one
[0016] (1) the raw material titanium dioxide (TiO 2 ), praseodymium oxide (Pr 6 o 11 ) and niobium oxide (Nb 2 o 5 ), according to the chemical formula (Pr 0.5 Nb 0.5 ) x Ti 1-x o 2 for preparation, among which x =0.5%, and carry out rolling ball milling with absolute ethanol as the medium, dry the powder after rolling ball milling for 24 hours to obtain mixed dry powder;
[0017] (2) Pre-burn the mixed dry powder obtained in step (1) in a muffle furnace for 4 hours, and the pre-fire temperature is 1100 o C, the atmosphere is an air atmosphere, after cooling with the furnace, add the pre-fired mixed dry powder to 8 wt% polyvinyl alcohol aqueous solution, and granulate to obtain pellets with uniform particle size;
[0018] (3) Utilize the abrasive tool that the pellets obtained in step (2) are compressed into small discs with a thickness of 1.2 mm and a diameter of 10 mm, and then the small discs are placed in a muffle furnace for debinding for 2 ho
Example Embodiment
[0020] Example two
[0021] (1) the raw material titanium dioxide (TiO 2 ), praseodymium oxide (Pr 6 o 11 ) and niobium oxide (Nb 2 o 5 ), according to the chemical formula (Pr 0.5 Nb 0.5 ) x Ti 1-x o 2 for preparation, among which x =1%, and carry out rolling ball milling with absolute ethanol as the medium, dry the powder after rolling ball milling for 24 hours to obtain mixed dry powder;
[0022] (2) Pre-burn the mixed dry powder obtained in step (1) in a muffle furnace for 4 hours, and the pre-fire temperature is 1100 o C, the atmosphere is an air atmosphere, after cooling with the furnace, add the pre-fired mixed dry powder to 8 wt% polyvinyl alcohol aqueous solution, and granulate to obtain pellets with uniform particle size;
[0023] (3) Utilize the abrasive tool that the pellets obtained in step (2) are compressed into small discs with a thickness of 1.2 mm and a diameter of 10 mm, and then the small discs are placed in a muffle furnace for debinding for 2 hour
Example Embodiment
[0025] Example three
[0026] (1) the raw material titanium dioxide (TiO 2 ), praseodymium oxide (Pr 6 o 11 ) and niobium oxide (Nb 2 o 5 ), according to the chemical formula (Pr 0.5 Nb 0.5 ) x Ti 1-x o 2 for preparation, among which x =2.5%, and use absolute ethanol as the medium to carry out rolling ball milling, and dry the powder after rolling ball milling for 24 hours to obtain mixed dry powder;
[0027] (2) Pre-burn the mixed dry powder obtained in step (1) in a muffle furnace for 4 hours, and the pre-fire temperature is 1100o C, the atmosphere is an air atmosphere, after cooling with the furnace, add the pre-fired mixed dry powder to 8 wt% polyvinyl alcohol aqueous solution, and granulate to obtain pellets with uniform particle size;
[0028] (3) Utilize the abrasive tool that the pellets obtained in step (2) are compressed into small discs with a thickness of 1.2 mm and a diameter of 10 mm, and then the small discs are placed in a muffle furnace for debinding fo
PUM
Property | Measurement | Unit |
---|---|---|
Thickness | aaaaa | aaaaa |
Diameter | aaaaa | aaaaa |
Abstract
Description
Claims
Application Information
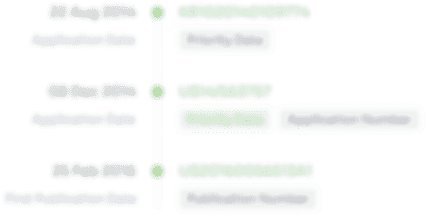
- R&D Engineer
- R&D Manager
- IP Professional
- Industry Leading Data Capabilities
- Powerful AI technology
- Patent DNA Extraction
Browse by: Latest US Patents, China's latest patents, Technical Efficacy Thesaurus, Application Domain, Technology Topic.
© 2024 PatSnap. All rights reserved.Legal|Privacy policy|Modern Slavery Act Transparency Statement|Sitemap