Method for treating diesel through hydrogenation
A hydrotreating and diesel technology, applied in hydrotreating process, treating hydrocarbon oil, chemical instruments and methods, etc., can solve problems such as poor selectivity of monocyclic aromatic hydrocarbons, improve activity and stability, prevent aggregation, and solve technical problems The effect of defects
- Summary
- Abstract
- Description
- Claims
- Application Information
AI Technical Summary
Problems solved by technology
Method used
Examples
Example Embodiment
[0079] Example 1
[0080] use figure 1 The shown process processes the diesel feedstock oil D. Diesel feedstock oil D enters the hydrogenation reactor from the feed oil inlet, and hydrogen enters the hydrogenation reactor from the hydrogen inlet. The first reaction zone and the second reaction zone are set up in the hydrogenation reactor from top to bottom, in the first reaction zone The hydrorefining catalyst A is filled, and the second reaction zone is filled with hydrorefining catalyst B. The reaction effluent I is discharged from the top of the hydrogenation reactor, and the reaction effluent II is discharged from the bottom of the hydrogenation reactor. The reaction effluent I and the reaction After the effluent II is mixed, it is separated to obtain hydrogenated oil. The hydrogenation reaction conditions and product properties are shown in Table 2. It can be seen from Table 2 that the saturation rate of polycyclic aromatic hydrocarbons in the hydrogenated oil is 85.1%, and
Example Embodiment
[0081] Example 2
[0082] use figure 1 The process shown treats the diesel feedstock oil E. Diesel feed oil E enters the hydrogenation reactor from the feed oil inlet, and hydrogen enters the hydrogenation reactor from the hydrogen inlet. The first reaction zone and the second reaction zone are set up in the hydrogenation reactor from top to bottom, in the first reaction zone The hydrorefining catalyst A is loaded, the hydrorefining catalyst C is loaded in the second reaction zone, the reaction effluent I is discharged from the top of the hydrogenation reactor, the reaction effluent II is discharged from the bottom of the hydrogenation reactor, and the reaction effluent I and the reaction After the effluent II is mixed, it is separated to obtain hydrogenated oil. The hydrogenation reaction conditions and product properties are shown in Table 2. It can be seen from Table 2 that the saturation rate of polycyclic aromatic hydrocarbons in the hydrogenated oil is 85.4%, and the select
PUM
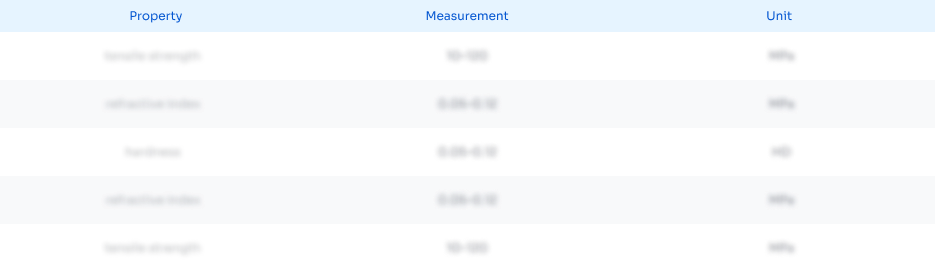
Abstract
Description
Claims
Application Information
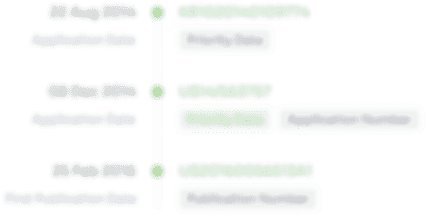
- R&D Engineer
- R&D Manager
- IP Professional
- Industry Leading Data Capabilities
- Powerful AI technology
- Patent DNA Extraction
Browse by: Latest US Patents, China's latest patents, Technical Efficacy Thesaurus, Application Domain, Technology Topic.
© 2024 PatSnap. All rights reserved.Legal|Privacy policy|Modern Slavery Act Transparency Statement|Sitemap