Error compensation method for bias temperature of fiber optical gyroscope
A technology of temperature error and fiber optic gyroscope, applied in the field of fiber optic inertia, can solve the problems of low precision of fiber optic gyroscope, inability to effectively compensate the temperature error of fiber optic gyroscope, and inability to reflect the temperature change of the fiber optic ring, and achieve the effect of improving accuracy
- Summary
- Abstract
- Description
- Claims
- Application Information
AI Technical Summary
Problems solved by technology
Method used
Image
Examples
Embodiment Construction
[0022] The method for compensating the zero bias temperature error of the fiber optic gyroscope includes the following steps:
[0023] Step A. Attach N temperature sensors 2 on the fiber ring 1 of the fiber optic gyroscope, wherein at least one temperature sensor 2 is attached to the inside of the fiber ring 1, and at least one temperature sensor 2 is attached to the outside of the fiber ring 1; 2≤N ≤5. When N is an even number, the temperature sensors 2 attached to the inner side of the optical fiber ring 1 and the outer side of the optical fiber ring 1 correspond to each other in spatial position. When N is an odd number, there is a one-to-one correspondence between the attachment of N−1 temperature sensors 2 on the inside and outside of the optical fiber ring 1 .
[0024] Step B. Establish the temperature error model of the fiber optic gyroscope:
[0025] in,
[0026]
[0027] K i1 ~K in 、dK i1 ~dK in is the coefficient of each temperature item corresponding to the
PUM
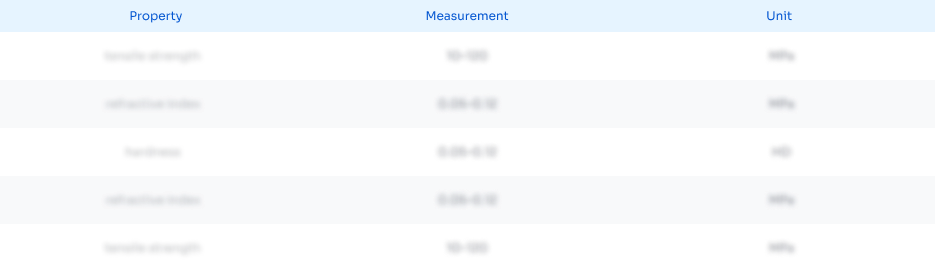
Abstract
Description
Claims
Application Information
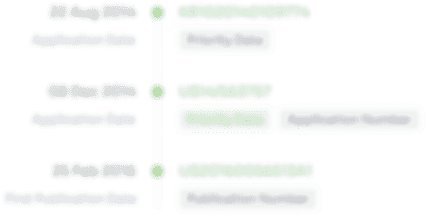
- R&D Engineer
- R&D Manager
- IP Professional
- Industry Leading Data Capabilities
- Powerful AI technology
- Patent DNA Extraction
Browse by: Latest US Patents, China's latest patents, Technical Efficacy Thesaurus, Application Domain, Technology Topic.
© 2024 PatSnap. All rights reserved.Legal|Privacy policy|Modern Slavery Act Transparency Statement|Sitemap