Method, device and system for measuring mechanical beam rigidity of capacitive MEMS accelerometer
A technology of accelerometer and measurement method, which is applied in the direction of speed/acceleration/shock measurement, measurement device, speed/acceleration/shock measurement equipment testing/calibration, etc. It can solve the problems of inability to accurately measure the stiffness of mechanical beams, etc., and achieve improvement The effect of measurement accuracy
- Summary
- Abstract
- Description
- Claims
- Application Information
AI Technical Summary
Benefits of technology
Problems solved by technology
Method used
Image
Examples
Embodiment Construction
[0044] In order to make the purpose, technical solution and advantages of the present application clearer, the present application will be further described in detail below in conjunction with the accompanying drawings and embodiments. It should be understood that the specific embodiments described here are only used to explain the present application, and are not intended to limit the present application.
[0045] In a specific application scenario of the method, device and system for measuring the mechanical beam stiffness of a capacitive MEMS accelerometer in this application:
[0046] The traditional technology proposes a method based on Hooke's law, by applying force to the inertial mass of the sensitive structure of the capacitive MEMS accelerometer, measuring the displacement of the inertial mass under the force, and then obtaining the capacitive MEMS acceleration according to Hooke's law The mechanical beam stiffness of the gauge. However, this method has at least the foll
PUM
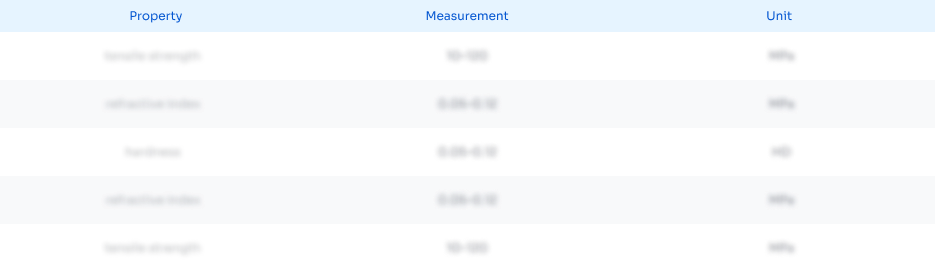
Abstract
Description
Claims
Application Information
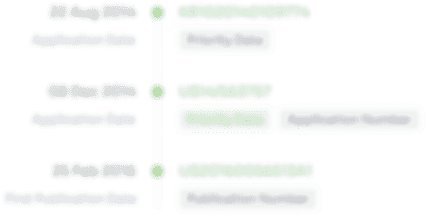
- R&D Engineer
- R&D Manager
- IP Professional
- Industry Leading Data Capabilities
- Powerful AI technology
- Patent DNA Extraction
Browse by: Latest US Patents, China's latest patents, Technical Efficacy Thesaurus, Application Domain, Technology Topic.
© 2024 PatSnap. All rights reserved.Legal|Privacy policy|Modern Slavery Act Transparency Statement|Sitemap