Bus seat bottom frame welding jig
A technology for welding fixtures and buses, applied in welding equipment, auxiliary welding equipment, welding/cutting auxiliary equipment, etc., can solve the problems of low welding efficiency, reduced welding efficiency, and prone to human errors, etc., to improve the clamping accuracy , Reduce the difficulty of welding, improve the effect of positioning effect
- Summary
- Abstract
- Description
- Claims
- Application Information
AI Technical Summary
Problems solved by technology
Method used
Examples
Embodiment 1
[0046] refer to figure 2 and image 3 , a bus seat bottom frame welding jig disclosed in the present invention includes a support plate 2 arranged in the vertical direction, a first positioning plate 3 arranged on the support plate 2, a reversible horizontally arranged on the support plate The second positioning plate 4 that cooperates with the first positioning plate 3 on the plate 2 and the pressing mechanism arranged on the supporting plate 2 .
[0047] refer to Figure 4 and Figure 5 The first positioning plate 3 is used to form a first assembly surface 31 on one side that is used to cooperate with the second positioning plate 4, and the first assembly surface 31 lateral sides are respectively provided with a first longitudinal positioning groove 311 for placing the longitudinal guide bar 12, and The lateral sides of the first assembly surface 31 are respectively provided with a first lateral notch 312 for placing the adjusting sliding sleeve 13, and the longitudinal ...
Embodiment 2
[0059] refer to Figure 9 and Figure 10 The difference between this embodiment and Embodiment 1 is that the bus seat bottom frame welding jig also includes a base 9, the support plate 2 is perpendicular to the base 9, and the support plate 2 is rotatable around the longitudinal central axis of the support plate 2 Set on the base 9, specifically, the bottom surface of the support plate 2 is fixedly connected with the connecting plate 22 by bolts, the connecting plate 22 is a U-shaped plate, the supporting plate 2 is inserted in the groove cavity of the connecting plate 22, and the bottom of the connecting plate 22 is welded and fixed There is a rotating shaft, and the base 9 is fixed with a turntable 23 that matches the rotation of the rotating shaft; with the above structure, when welding, only need to rotate the support plate 2, you can switch the welding position on the front and back, no need for the operator to walk around, not only easy to use , and can improve welding ...
PUM
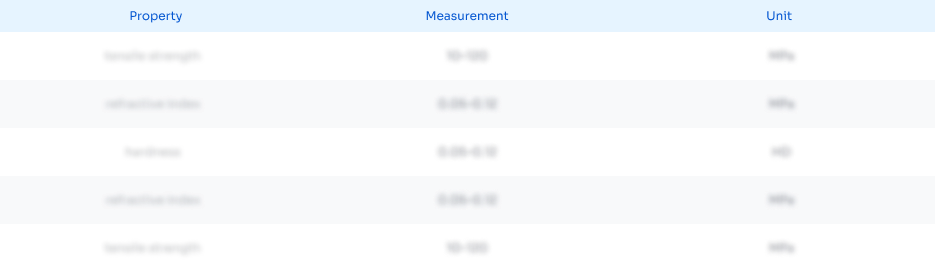
Abstract
Description
Claims
Application Information
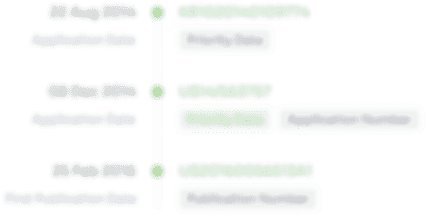
- R&D Engineer
- R&D Manager
- IP Professional
- Industry Leading Data Capabilities
- Powerful AI technology
- Patent DNA Extraction
Browse by: Latest US Patents, China's latest patents, Technical Efficacy Thesaurus, Application Domain, Technology Topic.
© 2024 PatSnap. All rights reserved.Legal|Privacy policy|Modern Slavery Act Transparency Statement|Sitemap