Wear-resistant ready-to-coat light film and preparation method thereof
A technology of light film and base film, which is applied in the field of wear-resistant and ready-to-coat light film and its preparation, can solve the problems that the light film is not easy to decompose, increase the production process, and aggravate white pollution, so as to achieve good market promotion value and economic benefits, save Raw materials, to achieve the effect of online synchronous completion
- Summary
- Abstract
- Description
- Claims
- Application Information
AI Technical Summary
Problems solved by technology
Method used
Examples
Example Embodiment
[0033] Example 1
[0034] This embodiment provides a wear-resistant and light-coating film, which is prepared by the following preparation method:
[0035] Prepare the dispersion of the auxiliary agent inside the base film: mix the self-emulsifying nano-scale silica powder (with a particle size of 20 nanometers) in a ratio of 5:95 to the demineralized water mass ratio, and stir for 30 minutes at 800 rpm Prepare the dispersion of the auxiliary agent inside the basement membrane; transfer the dispersion of the auxiliary agent inside the basement membrane to a storage tank and stir at a constant speed at a speed of 90 rpm for standby;
[0036] Basement membrane internal auxiliary agent dispersion and viscose collagen solution on-line mixing and spraying: According to the mass ratio of cellulose in the viscous collagen solution to the auxiliary agent in the basement membrane internal auxiliary agent dispersion of 1:0.1, the quantitative amount is transferred through the diaphragm pump Add
Example Embodiment
[0040] Example 2
[0041] This embodiment provides a wear-resistant and light-coating film, which is prepared by the following preparation method:
[0042] Preparing the internal auxiliary agent dispersion of the base film: mix the self-emulsifying nano-scale silica powder (with a particle size of 30 nanometers) in a ratio of 5:95 to the demineralized water mass ratio, and stir for 30 minutes at 800 rpm Prepare the dispersion of the auxiliary agent inside the basement membrane; transfer the dispersion of the auxiliary agent inside the basement membrane to a storage tank and stir at a constant speed at a speed of 90 rpm for standby;
[0043] Basement membrane internal auxiliary agent dispersion and preparation viscose collagen solution on-line mixing spray film: according to the mass ratio of the cellulose in the viscous collagen solution to the auxiliary agent in the basement membrane internal auxiliary agent dispersion of 1:0.15, the amount will be quantified by the diaphragm pump Add
Example Embodiment
[0047] Example 3
[0048] This embodiment provides a wear-resistant and light-coating film, which is prepared by the following preparation method:
[0049] Prepare the dispersion of the auxiliary agent inside the base film: mix the self-emulsifying nano-scale silica powder (with a particle size of 25 nanometers) in a ratio of 5:95 to the demineralized water mass ratio, and stir for 30 minutes at 800 rpm Prepare the internal auxiliary agent dispersion of the basement membrane; transfer the internal auxiliary agent dispersion of the basement membrane to a storage tank and stir at a constant speed at a speed of 90 rpm for standby;
[0050] Basement membrane internal auxiliary agent dispersion and viscose collagen solution on-line mixing spray film: according to the mass ratio of the cellulose in the viscous collagen solution to the auxiliary agent in the basement membrane internal auxiliary agent dispersion of 1:0.3, the quantitative Add the dispersion of the auxiliary agent inside the ba
PUM
Property | Measurement | Unit |
---|---|---|
Particle size | aaaaa | aaaaa |
Particle size | aaaaa | aaaaa |
Particle size | aaaaa | aaaaa |
Abstract
Description
Claims
Application Information
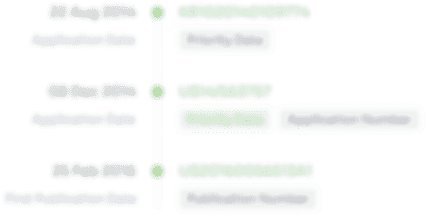
- R&D Engineer
- R&D Manager
- IP Professional
- Industry Leading Data Capabilities
- Powerful AI technology
- Patent DNA Extraction
Browse by: Latest US Patents, China's latest patents, Technical Efficacy Thesaurus, Application Domain, Technology Topic.
© 2024 PatSnap. All rights reserved.Legal|Privacy policy|Modern Slavery Act Transparency Statement|Sitemap