Three-phase 18/16-pole bearingless switched reluctance motor
A switched reluctance motor and bearingless technology, which is applied in the direction of electromechanical devices, electrical components, electric components, etc., can solve the problems of limited popularization and application, dead zone, and existence of starting torque, etc., and achieves the reduction of stator core loss and simple control , the effect of increasing the output power
- Summary
- Abstract
- Description
- Claims
- Application Information
AI Technical Summary
Benefits of technology
Problems solved by technology
Method used
Image
Examples
Embodiment Construction
[0025] The technical scheme of a three-phase 18 / 16 pole bearingless switched reluctance motor of the present invention will be described in detail below in conjunction with the accompanying drawings:
[0026] like figure 1 As shown, it is a three-dimensional structural schematic diagram of a three-phase 18 / 16 pole bearingless switched reluctance motor of the present invention, wherein, 1 is a stator, 2 is a suspension coil, 3 is a torque coil, 4 is a rotor, 5 is a rotating shaft, X, Y and Z are the three coordinate axes of the Cartesian coordinate system, respectively.
[0027] The three-phase bearingless switched reluctance motor includes a stator, a torque coil, a suspension coil, a rotor and a rotating shaft; the rotor is sleeved on the rotating shaft, and the rotor is arranged in the stator;
[0028] The stator has a salient pole structure, including 12 torque teeth and 6 suspension teeth, a total of 18 teeth; the 6 suspension teeth are evenly distributed in space, and t
PUM
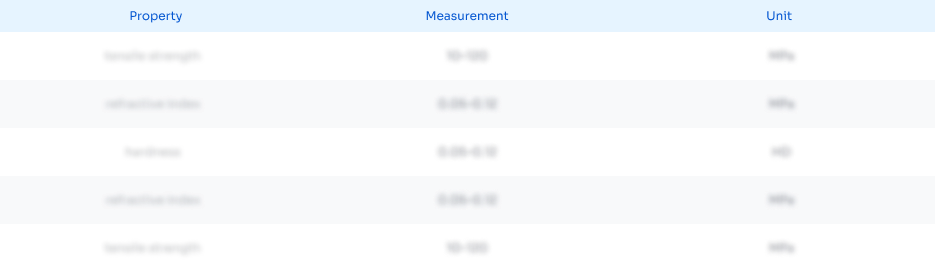
Abstract
Description
Claims
Application Information
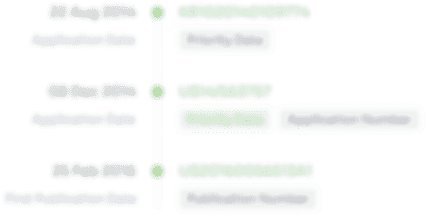
- R&D Engineer
- R&D Manager
- IP Professional
- Industry Leading Data Capabilities
- Powerful AI technology
- Patent DNA Extraction
Browse by: Latest US Patents, China's latest patents, Technical Efficacy Thesaurus, Application Domain, Technology Topic.
© 2024 PatSnap. All rights reserved.Legal|Privacy policy|Modern Slavery Act Transparency Statement|Sitemap