Autonomous charging method based on quadruped robot
A quadruped robot, self-charging technology, applied in instruments, current collectors, electric vehicles, etc., can solve the problem of lack of very mature self-charging methods, reduce the risk of accidental power failure, improve operating efficiency, and improve operating time. Effect
- Summary
- Abstract
- Description
- Claims
- Application Information
AI Technical Summary
Problems solved by technology
Method used
Image
Examples
Example Embodiment
[0030] In order to make the above characteristics and advantages of the present invention, it is more apparent to the following examples, and in line with the accompanying drawings, the present invention is not limited thereto.
[0031] Such as figure 1 As shown, a self-charging method based on four-foot robots, including the following steps:
[0032] First, generate charging pile positioning beacons for charging piles:
[0033] S01, the four-foot robot departs from the position of the charging pile, and the SLAM modeling service is used to build an inspected area map;
[0034] S02, extract the charging pile characteristics, create a tag dictionary for the charging pile;
[0035] S03, is identified by the four-legged robot to generate a charging pile positioning mark image; generate a QR code containing the poses information;
[0036] S04, outputting the charging pile position mark image as a charging pile positioning beacon, at the same time according to the charging pile positionin
PUM
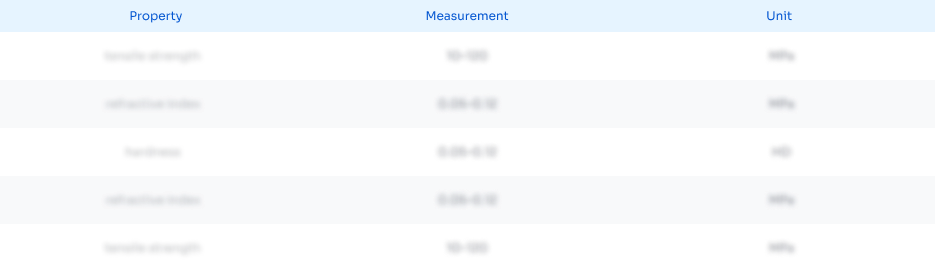
Abstract
Description
Claims
Application Information
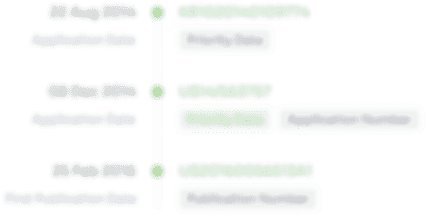
- R&D Engineer
- R&D Manager
- IP Professional
- Industry Leading Data Capabilities
- Powerful AI technology
- Patent DNA Extraction
Browse by: Latest US Patents, China's latest patents, Technical Efficacy Thesaurus, Application Domain, Technology Topic.
© 2024 PatSnap. All rights reserved.Legal|Privacy policy|Modern Slavery Act Transparency Statement|Sitemap