Unmanned railway coal leveling and compacting system and method
A coal and flat pressing technology, applied in transportation and packaging, loading/unloading, conveyors, etc., can solve the problems of rolling quality discount, prone to accidents, bumping into the car board, etc., to reduce the accident rate and improve work efficiency Effect
- Summary
- Abstract
- Description
- Claims
- Application Information
AI Technical Summary
Benefits of technology
Problems solved by technology
Method used
Image
Examples
Embodiment 1
[0023] This embodiment is an unmanned railway coal leveling and compacting system, such as figure 1 , 2 shown. This embodiment includes: being installed on the steel structure frame 1 and arranging the initial pressure swing beam 3 with the initial pressure roller 2 and the final pressure swing beam 5 with the final pressure roller 4 along the railway line, the described initial pressure swing beam and One end of the final pressure swing beam is hingedly connected with the steel structure frame respectively, and the other end is respectively connected with the initial pressure steel cable 6, the final pressure steel cable 7 and its initial pressure hoist 8, and the final pressure hoist 9. An initial pressure cable unloading device 101 and a final pressure cable unloading device 102 are provided; an initial pressure cabin position sensor 10 and a final pressure cabin position sensor 11 are provided on the side of the steel structure frame corresponding to the initial pressure rol
Embodiment 2
[0035] This embodiment is an improvement of the above-mentioned embodiment, and it is a refinement of the above-mentioned embodiment about the cable unloading device. The initial pressure cable unloading device and the final pressure cable unloading device described in this embodiment include: a travel motor 1011, the The walking motor is fixedly connected with the protection bracket 1012, and the protection bracket is connected with the swing beam hook 1013, as image 3 As shown (taking the initial pressure cable unloading device as an example, the final pressure cable unloading device is the same as the initial pressure cable unloading device).
[0036] The walking motor is a device capable of moving back and forth ( image 3 Move back and forth along the direction of arrow D), and drive the protective bracket to move back and forth. The swing beam hook is fixedly installed on the swing beam. When the swing beam is raised to the highest position (non-working state), the protec
Embodiment 3
[0039] This embodiment is an unmanned railway coal leveling and compacting method using the system described in the above embodiments. The method controls and adjusts the rolling force of the rolling rollers during the compaction process by predicting the rolling force. Strive to compact the top of the material pile flat during the two rolling processes. The method also has a learning function, and continuously optimizes the rolling process in the process of continuously accumulating experience. The entire rolling process can be fully automated, and human intervention can be set up for safety at necessary work points (such as the front of the car entering), or it can be fully automated.
[0040] The specific steps of the method described in this embodiment are as follows:
[0041] Step 1, the loading process starts: after the system is started, conduct a self-inspection, and confirm that the initial pressure roller and the final pressure roller are at the highest position and in
PUM
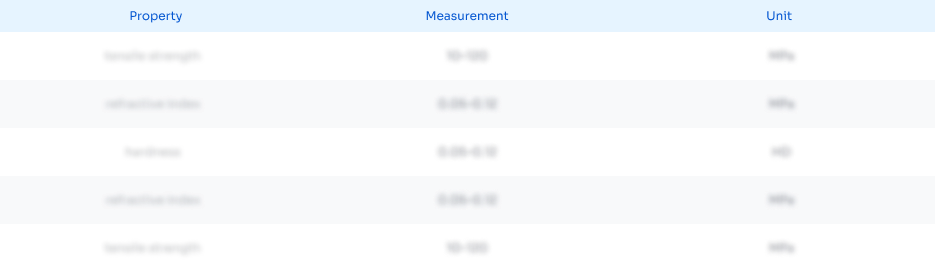
Abstract
Description
Claims
Application Information
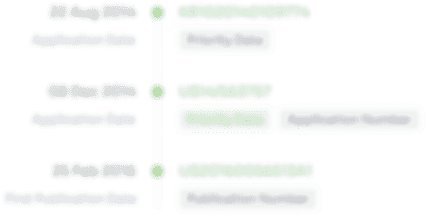
- R&D Engineer
- R&D Manager
- IP Professional
- Industry Leading Data Capabilities
- Powerful AI technology
- Patent DNA Extraction
Browse by: Latest US Patents, China's latest patents, Technical Efficacy Thesaurus, Application Domain, Technology Topic.
© 2024 PatSnap. All rights reserved.Legal|Privacy policy|Modern Slavery Act Transparency Statement|Sitemap