Preparation method of tetraalkylthiuram monosulfide
A technique for sulfiding tetraalkylthiuram and monohydric alcohols, which is applied in the direction of organic chemistry, can solve the problems of violent reaction of sodium cyanide, high residue of tetramethylthiuram disulfide, difficulty in separation and treatment, etc., and improve the product quality. Yield and quality, the realization of circular economy development, the effect of high operational safety
- Summary
- Abstract
- Description
- Claims
- Application Information
AI Technical Summary
Benefits of technology
Problems solved by technology
Method used
Examples
Embodiment 1
[0026] Put 80.0g of water, 50.0g of ethanol, and 36.4g of carbon disulfide into a four-necked flask with a condenser in turn at room temperature, cool down to 10-15°C, and stir at this temperature for 2.5h; control the temperature to 10-15°C and dropwise add 50.0 g dimethylamine (wt40%) aqueous solution, after the completion, the temperature was slowly raised to 15~20℃ and reacted for 1.5h; 63.8g hydrogen peroxide (wt13%) was added dropwise at a controlled temperature of 15~20℃, and stirred for 2.5h after the dropwise addition was completed; Add 37.2g of sodium cyanide (wt27.5%) aqueous solution dropwise at ~20°C, stir for 1.5h after the dropwise addition, control the temperature to 15~20°C and dropwise add 19.9g of triphenylphosphine (wt17.5%) alcohol solution, dropwise After adding, stir for 3.5h; filter, dry and pulverize to obtain 45.7g of tetramethylthiuram monosulfide, the mother liquor is recovered and separated by-products sodium thiocyanate and triphenylphosphine sulfur;
Embodiment 2
[0028] Put 80.0g of water, 53.0g of methanol, and 53.4g of carbon disulfide into a four-necked flask with a condenser in turn at room temperature, cool down to 10-15°C, and stir at this temperature for 2.5h; control the temperature to 10-15°C and dropwise add 50.0 g diethylamine solution, slowly heat up to 15~20℃ for 1.5h after completion; add 83.5g hydrogen peroxide (wt 15%) dropwise at a controlled temperature of 15~20℃, stir for 2.5h after the dropwise addition; control the temperature at 15~20℃ Add 56.0g sodium cyanide (wt27.5%) aqueous solution, stir for 1.5h after the dropwise addition; control the temperature to 15~20℃ and add dropwise 50.2g triphenylphosphine (wt17.5%) alcohol solution, stir after the dropwise addition 3.5h; filter, dry and pulverize to obtain 87.3g of tetraethylthiuram monosulfide, the mother liquor was recovered and separated by-products sodium thiocyanate and triphenylphosphine sulfur; the yield of tetramethylthiuram monosulfide was 98.6%, Liquid phase
Embodiment 3
[0030] Put 80.0g of water, 55.0g of isopropanol and 31.1g of carbon disulfide into a four-necked flask with a condenser in turn at room temperature, cool down to 10-15°C, and stir at this temperature for 2.5h; control the temperature to 10-15°C dropwise Add 50.0g of diisobutylamine solution, slowly heat up to 15~20℃ and react for 1.5h after completion; control the temperature to 15~20℃, add 48.1g hydrogen peroxide (wt15%) dropwise, stir for 2.5h after the dropwise addition; control the temperature to 15~20℃ 49.9g sodium cyanide (wt27.5%) aqueous solution was added dropwise at 20°C, stirred for 1.5h after the dropwise addition; 34.1g triphenylphosphine (wt17.5%) alcohol solution was added dropwise at a temperature of 15-20°C After completion, stir for 3.5h; filter, dry and pulverize to obtain 70.5g of tetraisobutylthiuram monosulfide, the mother liquor is recovered and separated by-products sodium thiocyanate, triphenylphosphine sulfur; tetraisobutylthiuram monosulfide The yield w
PUM
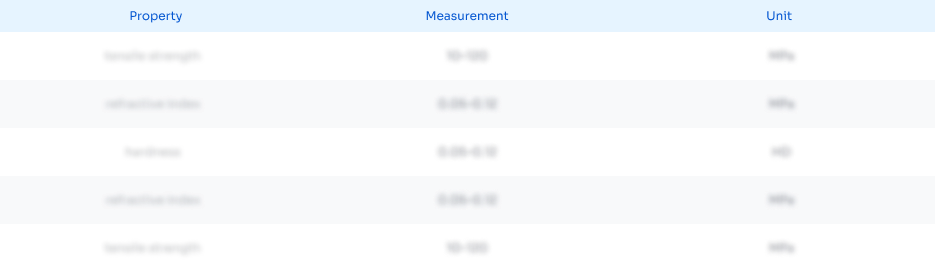
Abstract
Description
Claims
Application Information
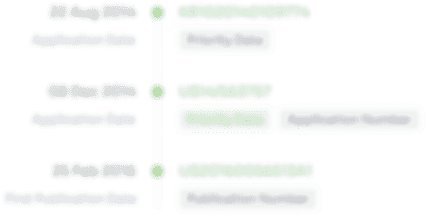
- R&D Engineer
- R&D Manager
- IP Professional
- Industry Leading Data Capabilities
- Powerful AI technology
- Patent DNA Extraction
Browse by: Latest US Patents, China's latest patents, Technical Efficacy Thesaurus, Application Domain, Technology Topic.
© 2024 PatSnap. All rights reserved.Legal|Privacy policy|Modern Slavery Act Transparency Statement|Sitemap