Thermal print assembly
- Summary
- Abstract
- Description
- Claims
- Application Information
AI Technical Summary
Benefits of technology
Problems solved by technology
Method used
Examples
Example
Example 1
[0078] Print Assembly I-1P includes a dye-receiving layer and a dye-donor layer. The dye-receiving layer was made of CAP-482-20 prepared by dissolving 5.04 gm of CAP-482-20 in 74.96 gm of dichloromethane, coating the solution onto a 100-micron thick Estar® polyester support at a dry thickness coverage of 5 microns, and drying at room temperature. The dye-donor layer was made by dissolving 5.04 gm of polymer PC-1 in 74.96 gm of dichloromethane, adding 0.24 gm of the dye Magenta #1, whose structure is given below, coating the solution onto the dried dye-receiving layer at a dry thickness coverage of 5 microns, drying overnight at room temperature, and then drying at 60° C. for several hours.
[0079] The dye was partitioned between the dye-donor layer and the dye-receiving layer by placing the print assembly between two heated platens and holding the assembly at 140° C. under a pressure of 0.35 to 0.70 MPa for 10 minutes. The print assembly was removed from between the heated pl
Example
Example 2
Dye-Donor Element I-1
[0087] A dye-donor element was prepared by coating the following layers in the order recited on a first side of a 4.5 micron poly(ethylene terephthalate) support:
[0088] (1) a subbing layer of a titanium alkoxide (Tyzor TBT® from E.I DuPont de Nemours and Company) (0.16 g / m2) from n-propyl acetate and n-butyl alcohol solvent mixture, and
[0089] (2) a dye-donor layer containing the cyan dyes illustrated below in the following amounts: cyan dye #1 at 0.093 g / m2, cyan dye #2 at 0.084 g / m2, and cyan dye #3 at 0.21 g / m2; ethyl cellulose (EC-461, Scientific Polymer Products, Inc.) binder at 0.22 g / m2; and divinyl benzene beads at 0.0084 g / m2 coated from a solvent mixture of 75 wt. % toluene, 20 wt. % methanol, and 5 wt. % cyclopentanone.
[0090] Dye donor element I-1 contains, in addition to the cyan dye #1 found in Table 1, two additional cyan dyes having similar structures and solubilities.
[0091] On a second side of the support, a slipping laye
Example
Example 3
Dye-Donor Element I-9
[0101] A dye-donor element was prepared the same as dye-donor element I-1 except that the dye-donor layer contained the magenta dyes illustrated below as follows: Magenta dye #1 at 0.0700 g / m2, Magenta dye #2 at 0.0642 g / m2, and Magenta dye #3 at 0.1462 g / m2, ethyl cellulose (Ethocel 45, Dow Chemical Company) binder at 0.2967 g / m2, and 2 micron divinyl benzene beads at 0.0054 g / m2 coated from a solvent mixture of 75 wt. % toluene, 20 wt. % methanol and 5 wt. % cyclopentanone.
[0102] Dye donor element I-9 contains, in addition to the magenta dyes #1 and #3 found in Table 1, one additional magenta dye having similar structure and solubility.
Dye-Donor Elements I-10 Through I-13 and Comparative Element C-5
[0103] Dye-donor elements I-10 through I-13 and comparative element C-5 were prepared the same as dye-donor element I-9, except that the ethyl cellulose (Ethocel 45) in the dye-donor layer was replaced by the polymers listed in Table 4.
Proc
PUM
Property | Measurement | Unit |
---|---|---|
Fraction | aaaaa | aaaaa |
Time | aaaaa | aaaaa |
Density | aaaaa | aaaaa |
Abstract
Description
Claims
Application Information
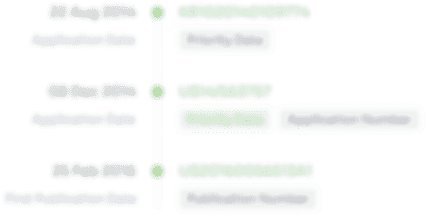
- R&D Engineer
- R&D Manager
- IP Professional
- Industry Leading Data Capabilities
- Powerful AI technology
- Patent DNA Extraction
Browse by: Latest US Patents, China's latest patents, Technical Efficacy Thesaurus, Application Domain, Technology Topic.
© 2024 PatSnap. All rights reserved.Legal|Privacy policy|Modern Slavery Act Transparency Statement|Sitemap