Turbine Vane Securing Mechanism
a technology of securing mechanism and turbine vane, which is applied in the direction of machines/engines, liquid fuel engines, other chemical processes, etc., can solve the problems of reducing the useful life of the turbine vane and causing wear
- Summary
- Abstract
- Description
- Claims
- Application Information
AI Technical Summary
Benefits of technology
Problems solved by technology
Method used
Image
Examples
Embodiment Construction
[0019]As shown in FIGS. 1-8, this invention is directed to a turbine vane attachment system 10 configured to eliminate movement of a turbine vane 12 relative to a turbine vane carrier 14 during turbine engine operation. The turbine vane attachment system 10 is usable with turbine vanes 12 in the turbine and compressor sections of a turbine engine. The turbine vane attachment system 10 may include a base 16 attached to a turbine airfoil 18. The base 16 may be configured to contact a wedge support 20 along a plane 22 that is generally nonparallel and nonorthogonal with a longitudinal axis 23 of the airfoil 18. A connection system 82, such as, but not limited to, a bolt 24 may connect the base 16 with the wedge support 20. As the bolt 24 is advanced, a distance between a channel 26 in the base 16 and an outer bearing surface 28 increases. The turbine vane 12 may be positioned in a vane carrier 30 such that tongues 32 extending from the vane carrier 30 are positioned in the channels 26. As
PUM
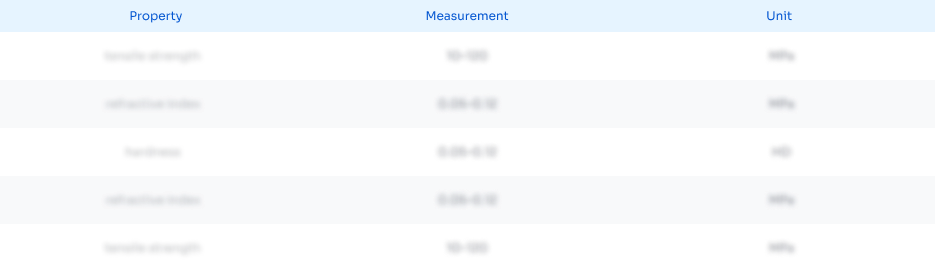
Abstract
Description
Claims
Application Information
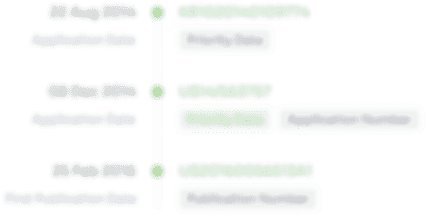
- R&D Engineer
- R&D Manager
- IP Professional
- Industry Leading Data Capabilities
- Powerful AI technology
- Patent DNA Extraction
Browse by: Latest US Patents, China's latest patents, Technical Efficacy Thesaurus, Application Domain, Technology Topic.
© 2024 PatSnap. All rights reserved.Legal|Privacy policy|Modern Slavery Act Transparency Statement|Sitemap