Variable plate heat exchangers
a heat exchanger and variable plate technology, applied in the field of plate heat exchangers, can solve the problems that traditional plate heat exchangers do not lend themselves to the concepts of ‘variable volume’ or ‘variable heat flux’, and achieve the effect of superior capabilities
- Summary
- Abstract
- Description
- Claims
- Application Information
AI Technical Summary
Benefits of technology
Problems solved by technology
Method used
Examples
Embodiment Construction
The Variable Plate Heat Exchanger
[0056]The considerations and solutions for this new variable plate design are discussed in the section below.
(a) Variable Plate—Variable Volume
[0057]Traditional plate heat exchangers are made up with plate packs where the individual plates in a given plate pack have common plate spacings (although several different types of plate pack may be fitted within the same heat exchanger frame).[0058]The preferred design of the present disclosure uses a plate pack which has two or more different plate spacings within it. Also the process conduit can pass directly though the heat transfer plate and, if necessary, this can be achieved without welds or seals on the inter plate conduit. Alternatively, the process conduit can be diverted into or out of the plate at any point in the plate stack. Also the heat transfer fluid conduit can be fed to each plate from the outside and does not need to pass through a space which is sealed from but surrounded by process mate...
PUM
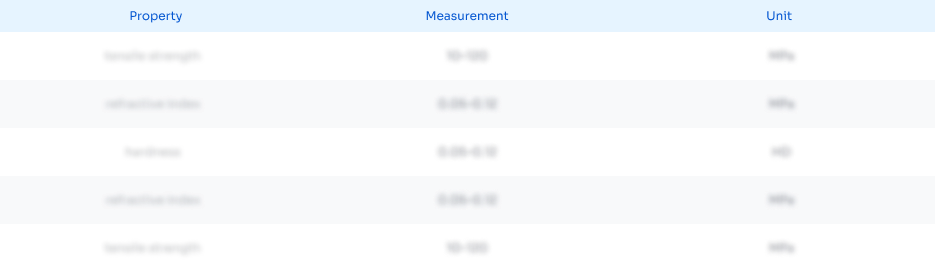
Abstract
Description
Claims
Application Information
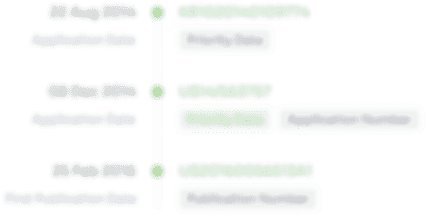
- R&D Engineer
- R&D Manager
- IP Professional
- Industry Leading Data Capabilities
- Powerful AI technology
- Patent DNA Extraction
Browse by: Latest US Patents, China's latest patents, Technical Efficacy Thesaurus, Application Domain, Technology Topic.
© 2024 PatSnap. All rights reserved.Legal|Privacy policy|Modern Slavery Act Transparency Statement|Sitemap