Cold wind generation from slag heat
a technology of slag heat and cold wind, which is applied in the direction of furnaces, lighting and heating apparatus, machines/engines, etc., can solve the problems of large cosub>2 /sub>emission of conversion of carbon compounds, and very largely lost sensible heat of blast furnace gas, etc., to save external energy, simplify operation, and reduce costs
- Summary
- Abstract
- Description
- Claims
- Application Information
AI Technical Summary
Benefits of technology
Problems solved by technology
Method used
Image
Examples
Embodiment Construction
[0040]Various embodiments of this heat recovery and use for generating cold-air blast are explained below with reference to FIG. 1:
[0041]The liquid, hot slag 10 which is obtained periodically during each tapping operation is cooled by introduction of a cold solid 12 in a granulation installation 14 and solidifies, wherein the resultant hot solids mixture still has the highest possible temperature which is substantially limited by the subsequent processing of the mixture.
[0042]Cold, vitreously solidified blast furnace slag may, for example, be used as the cold solid. Using cold blast furnace slag has the advantage that, after the introduction thereof into the liquid slag, a homogeneous hot solids mixture is obtained.
[0043]Additionally or alternatively, however, spherical or similarly shaped metal bodies, preferably of iron or steel, may also be used as the cold solid. On introduction into the liquid slag, the metal bodies bring about more rapid solidification of the liquid slag and so i
PUM
Property | Measurement | Unit |
---|---|---|
Temperature | aaaaa | aaaaa |
Temperature | aaaaa | aaaaa |
Temperature | aaaaa | aaaaa |
Abstract
Description
Claims
Application Information
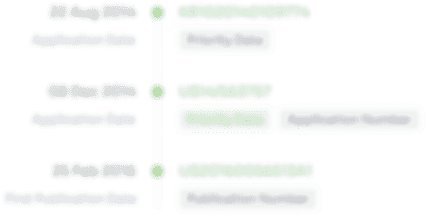
- R&D Engineer
- R&D Manager
- IP Professional
- Industry Leading Data Capabilities
- Powerful AI technology
- Patent DNA Extraction
Browse by: Latest US Patents, China's latest patents, Technical Efficacy Thesaurus, Application Domain, Technology Topic.
© 2024 PatSnap. All rights reserved.Legal|Privacy policy|Modern Slavery Act Transparency Statement|Sitemap