Non-pneumatic tire
a non-pneumatic and tire technology, applied in the field of vehicle tires and non-pneumatic tires, can solve the problems of reducing the service life of conventional pneumatic tires, requiring compressed fluid, and reducing the service life of pneumatic tires
- Summary
- Abstract
- Description
- Claims
- Application Information
AI Technical Summary
Benefits of technology
Problems solved by technology
Method used
Examples
fourth embodiment
[0052]FIGS. 12-13 illustrates a spoke disk 1000. The spoke disk 1000 has an axial thickness A substantially less than the axial thickness AW of the non-pneumatic tire. The spoke disk 1000 has a plurality of spokes that connect an inner ring 1010 to an outer ring 1020. The shear band 300 is mounted radially outward of the spoke disks. The spoke disk 1000 has a first spoke 1030 that is linear and joins the outer ring 1020 to the inner ring 1010. The first spoke 1030 forms an angle Beta with the outer ring 1020 in the range of 20 to 80 degrees. Beta is preferably less than 90 degrees. The spoke disk 1000 further includes a second spoke 1040 that extends from the outer ring 1020 to the inner ring 1010, preferably in a curved shape. The second spoke 1040 is joined with the first spoke 1030 at a junction 1100. The curved spoke 1040 has a first curvature from the outer ring to the junction 1100, and a second curvature from the junction to the inner ring 1010. In this example, the first cur...
fifth embodiment
[0054]FIG. 14 illustrates a spoke disk 2000, which is similar to the spoke disk 1000, except for the following differences. The spoke disk 2000 has a first and second spoke 2030, 2040 which are joined together by a junction 2100, forming two approximate triangular shapes A,B, that have curved boundaries. Both the first and second spokes 2030,2040 extend from an outer ring 2020 to an inner ring 2010. Both the first and second spokes 2030, 2040 are curved. The curve of the outer radial portion L2 of each spoke has a first curvature, and the inner radial portions L1 have a curve in the opposite direction of the first curvature. FIG. 15 illustrates the spoke disk 2000 buckling under load. The radially outer portions of 2040,2030 buckle in the angular direction.
[0055]A preferred embodiment of a non-pneumatic tire is shown in FIG. 1B. The spoke disks on the outer axial ends are the spoke disks 400, and are oriented so that they buckle axially outward. Located between the opposed spoke dis...
PUM
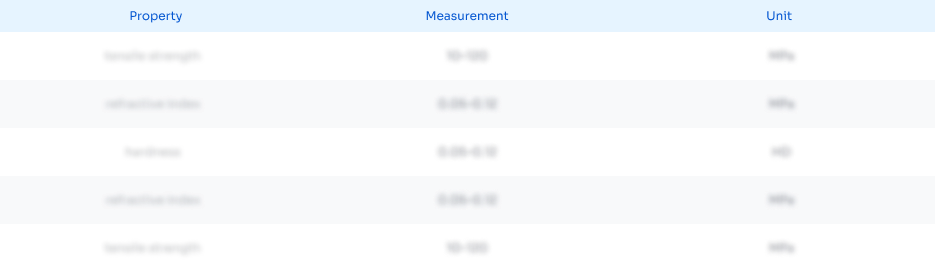
Abstract
Description
Claims
Application Information
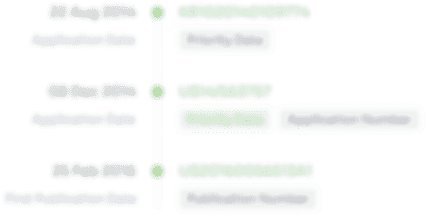
- R&D Engineer
- R&D Manager
- IP Professional
- Industry Leading Data Capabilities
- Powerful AI technology
- Patent DNA Extraction
Browse by: Latest US Patents, China's latest patents, Technical Efficacy Thesaurus, Application Domain, Technology Topic.
© 2024 PatSnap. All rights reserved.Legal|Privacy policy|Modern Slavery Act Transparency Statement|Sitemap