Finishing device
- Summary
- Abstract
- Description
- Claims
- Application Information
AI Technical Summary
Benefits of technology
Problems solved by technology
Method used
Image
Examples
Example
[0037]In the figures, the same elements, or elements that correspond with one another, are identified with the same reference numbers and are therefore not described again unless it is useful to do so. The disclosures contained in the overall description are logically analogous and convertible to the same parts that have the same reference numbers or the same component names. Also, the positional information selected in the description, such as top, bottom, side, etc., refer to the figure directly described and shown and are logically convertible to the new position when a positional change is made. Furthermore, individual features or featural combinations from the various exemplary embodiments shown and described can represent independent, inventive solutions in their own right or according to this invention.
[0038]In FIG. 1, the finishing device 1 according to the invention is shown schematically. The frame to be machined 4, which is a window frame here, lies on a support surface 10 o
PUM
Property | Measurement | Unit |
---|---|---|
Angle | aaaaa | aaaaa |
Abstract
Description
Claims
Application Information
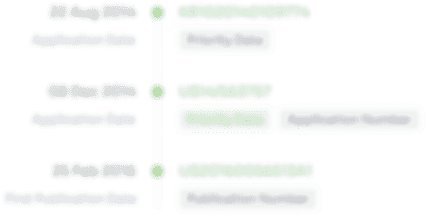
- R&D Engineer
- R&D Manager
- IP Professional
- Industry Leading Data Capabilities
- Powerful AI technology
- Patent DNA Extraction
Browse by: Latest US Patents, China's latest patents, Technical Efficacy Thesaurus, Application Domain, Technology Topic.
© 2024 PatSnap. All rights reserved.Legal|Privacy policy|Modern Slavery Act Transparency Statement|Sitemap