Production method for stator
- Summary
- Abstract
- Description
- Claims
- Application Information
AI Technical Summary
Benefits of technology
Problems solved by technology
Method used
Image
Examples
Example
Example 1
[0061]An amorphous plate (thickness: 25 μm, crystallization temperature: 391° C., degree of crystallinity: 0%, tensile strength: 1861 MN / m2) was prepared, the amorphous plate was punched with use of a press die, and thus, stator core plates were produced. Since the amorphous-based soft magnetic material was used for the stator core plates, the degree of crystallinity thereof was 0%. The crystallization temperature was identified by measurement of the exothermic reaction starting temperature with use of a differential scanning calorimeter (DSC) under the condition in which the heating rate was 0.67 Ks−1.
[0062]Next, the stator core plates were stacked, were fastened with bolts, and thus, a stacked body was produced. In addition, insulators were inserted in slots of the stacked body.
[0063]Next, as illustrated in FIGS. 4(A) and 4(B), a plurality of stacked segments were inserted in the slots, the lead portions thereof were bent, and the adjacent lead portions were welded togethe
Example
Example 2
[0066]A nanocrystal plate (thickness: 25 μm, degree of crystallinity: 90%, tensile strength: 1820 MN / m2) was prepared, and the nanocrystal plate was punched into a stator core plate with use of a press die.
[0067]The degree of crystallinity thereof was calculated, by Expression (1), from a caloric value (J / g) of crystallization measured with a differential scanning calorimeter (DSC). As the “amorphous-based soft magnetic material which corresponds to a soft magnetic material to be measured”, an amorphous plate (i.e. the amorphous plate used in Example 1) before heat treatment of the nanocrystal plate (heat treatment for generating a nanocrystal) was used.
[0068]The stator core plates thus obtained were used and heated at 430° C. for three seconds. Except for this, the same process as Example 1 was performed to produce a stator.
[0069]In the present example, no breakage was generated when the coils were mounted, and a stator having the saturation magnetization improved by the
PUM
Property | Measurement | Unit |
---|---|---|
Degree of crystallinity | aaaaa | aaaaa |
Temperature | aaaaa | aaaaa |
Frequency | aaaaa | aaaaa |
Abstract
Description
Claims
Application Information
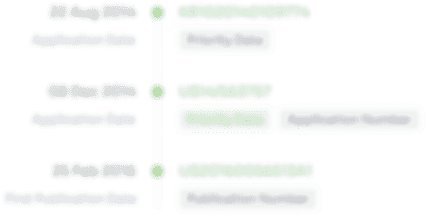
- R&D Engineer
- R&D Manager
- IP Professional
- Industry Leading Data Capabilities
- Powerful AI technology
- Patent DNA Extraction
Browse by: Latest US Patents, China's latest patents, Technical Efficacy Thesaurus, Application Domain, Technology Topic.
© 2024 PatSnap. All rights reserved.Legal|Privacy policy|Modern Slavery Act Transparency Statement|Sitemap