Process for producing hydrocarbons
a hydrocarbon and hydrocarbon oil technology, applied in the field of hydrocarbon oil production, can solve the problem that the equipment in the oil refinery is not designed to handle such materials
- Summary
- Abstract
- Description
- Claims
- Application Information
AI Technical Summary
Benefits of technology
Problems solved by technology
Method used
Image
Examples
example 1
Acid Degumming of Carinata Oil
[0253]Acid degumming of Brassica carinata oil is carried out by treating 100 g of the oil with 1 wt % phosphoric acid (85 wt-%) at 80° C. temperature for 30 min, whereby gums are separated / precipitated and then removed by centrifuging. The phosphorus value of the degummed oil is lower than 15 ppm.
example 2
Hydrolysis of Degummed Carinata Oil
[0254]The degummed oil obtained in example 1 is directed to hydrolysis, where the degummed oil is treated with 50 wt % of water under a pressure of 42 bars and a temperature of 250° C. in a tubular reactor, for 1.5 hours, to obtain an aqueous stream comprising glycerol and a stream comprising fatty acids (=pretreated feedstock).
example 3
Hydroprocessing Pretreated Feedstock
[0255]The pretreated feedstock obtained in example 2 is directed to one-step hydroprocessing, where the pretreated feedstock is hydroprocessed at 350-400° C. temperature, under 90 bar pressure, in the presence of a catalyst comprising NiW and NiMo, with hydrogen to obtain an effluent consisting of liquid phase and gas phase. Gas phase and water are separated and a phase comprising liquid hydrocarbons is obtained. Heavy hydrocarbons having carbon number of at least C20 (those boiling in the range from and above 320° C.) are separated by distillation (=hydroprocessed feedstock) and this hydroprocessed feedstock is directed to fluid catalytic cracking.
Example 4
Fluid Catalytic Cracking of Hydroprocessed Feedstock
[0256]Vacuum gas oil (90 vol-%) originating from crude oil is combined with the hydroprocessed feedstock (10 vol-%) obtained in example 3 to obtain a mixture, which is heated to a temperature of 370° C. and directed to fluid catalytic cracking re
PUM
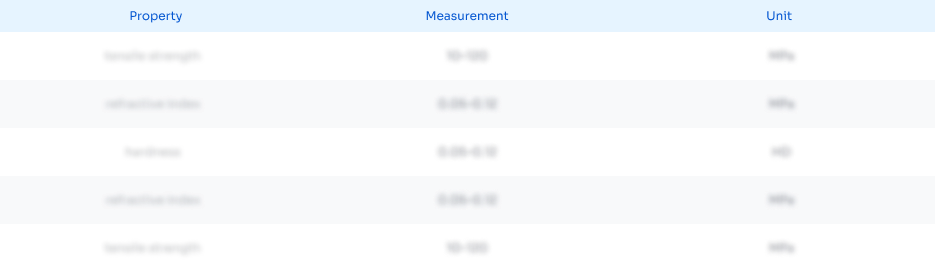
Abstract
Description
Claims
Application Information
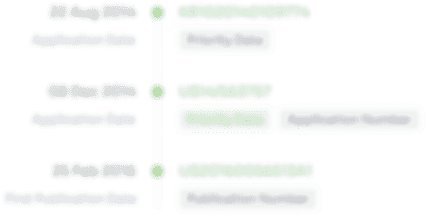
- R&D Engineer
- R&D Manager
- IP Professional
- Industry Leading Data Capabilities
- Powerful AI technology
- Patent DNA Extraction
Browse by: Latest US Patents, China's latest patents, Technical Efficacy Thesaurus, Application Domain, Technology Topic.
© 2024 PatSnap. All rights reserved.Legal|Privacy policy|Modern Slavery Act Transparency Statement|Sitemap