Continuous casting method for producing round blank with diameter larger than Phi800m on straight continuous casting machine
A continuous casting machine and round billet technology, which is applied to casting equipment, casting molten material containers, manufacturing tools, etc., can solve the problems of crusting and solidification of molten steel on the surface of the crystallizer, segregation and loosening of billet center, and unsatisfactory heat preservation effect, etc., to achieve Improve the heat transfer process of molten steel and improve the effect of purity
- Summary
- Abstract
- Description
- Claims
- Application Information
AI Technical Summary
Benefits of technology
Problems solved by technology
Method used
Image
Examples
Embodiment Construction
[0041] see figure 1 , the specific process steps of the continuous casting method for producing diameter ≥ φ800mm round billet on the straight continuous casting machine that the present invention relates to are as follows:
[0042] The implementation is carried out on a single-strand straight continuous casting machine. The specification of the specific production round billet is φ800mm, and the variety is 42CrMo, 15CrMoG, 12Cr1MoVG and other alloy steel types.
[0043]100-120 tons of molten steel from the steelmaking furnace is poured into the ladle, and after being refined in the ladle furnace and vacuum degassed in the vacuum degassing furnace, it is hoisted to the ladle turret of the continuous casting machine by a crane, and transferred to the tundish through the ladle turret Above, molten steel is injected into the impact area of the tundish through the nozzle at the bottom of the ladle. The impact area of the tundish is connected with the pouring area by a flow steel
PUM
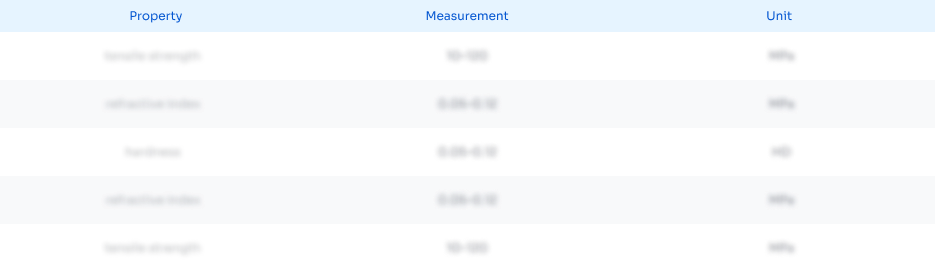
Abstract
Description
Claims
Application Information
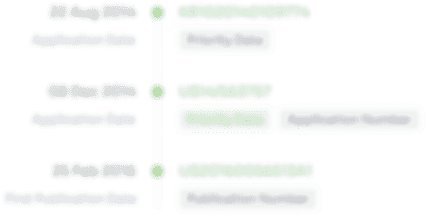
- R&D Engineer
- R&D Manager
- IP Professional
- Industry Leading Data Capabilities
- Powerful AI technology
- Patent DNA Extraction
Browse by: Latest US Patents, China's latest patents, Technical Efficacy Thesaurus, Application Domain, Technology Topic.
© 2024 PatSnap. All rights reserved.Legal|Privacy policy|Modern Slavery Act Transparency Statement|Sitemap