Nanocomposite microcapsules for self-healing of composite articles
a composite material and nano-composite technology, applied in the field of self-healing composite materials, can solve the problems of localized damage in the composite laminate, compromising the structural integrity, and prone to damage to composite materials such as wind turbines, aircraft parts,
- Summary
- Abstract
- Description
- Claims
- Application Information
AI Technical Summary
Benefits of technology
Problems solved by technology
Method used
Examples
example 1
Preparation of Nanoparticle-Induced Microcapsules
[0046]To manufacture the self-healing microcapsules, a beaker with 50 ml deionized water was placed on a hot plate. Then, 12.18 ml of 2.5 wt % aqueous solution of Ethylene Maleic Anhydride (EMA) was added to the beaker under high speed stirring between 800-1000 rpm. These stirring speeds have been chosen to accommodate the nanoparticles inside the microspheres. Simultaneously, 1.25g of urea, 0.125 g of ammonium chloride, and 0.125 g of resorcinol were added to this solution. The pH of the solution was raised from 3.12 to 3.50 by adding sodium hydroxide. A drop of 1 octanol was added to prevent surface bubbles. A slow stream of 14.75 g of dicyclopentadiene, which is the healing agent, was then added to this solution and was allowed to stabilize for 5 minutes. After adding dicyclopentadiene, 0.3 g of graphene nanoflakes (aka nanoparticles) was added to the solution. After stabilization, 3.1875 g of formaldehyde was added to the solution...
example 2
Manufacturing of Composite Panels
[0053]The microcapsules with graphene nanoparticles prepared in Example 1 above, were then mixed into an epoxy resin using ultrasonication and high speed stirring. The microcapsules with graphene nanoparticles were first cooled in an ice bath. A drying agent was added and the capsules were washed with a solvent to remove excess EMA surfactant. The solution was then centrifuged to separate the capsules, and then allowed to dry for 0-30 minutes. The microcapsules were then mixed into the epoxy matrix using high speed stirring and ultrasonication.
[0054]We have prepared composite panels using 2 wt %, 4 wt %, and 6 wt % of the nanoparticle-containing microcapsules in the epoxy resin. We have observed that the panel with 2 wt % of the nanoparticle-containing microcapsules increased the tensile strength by 31.51%. The panel with 4 wt % of nanoparticle-containing microcapsules in epoxy showed no improvement when compared to the baseline panel. The composite ...
PUM
Property | Measurement | Unit |
---|---|---|
temperature | aaaaa | aaaaa |
volume fraction | aaaaa | aaaaa |
surface-to-surface dimension | aaaaa | aaaaa |
Abstract
Description
Claims
Application Information
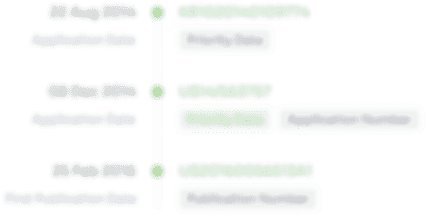
- R&D Engineer
- R&D Manager
- IP Professional
- Industry Leading Data Capabilities
- Powerful AI technology
- Patent DNA Extraction
Browse by: Latest US Patents, China's latest patents, Technical Efficacy Thesaurus, Application Domain, Technology Topic.
© 2024 PatSnap. All rights reserved.Legal|Privacy policy|Modern Slavery Act Transparency Statement|Sitemap