Anisotropic light-diffusing film, anisotropic light-diffusing laminate, anisotropic light-reflecting laminate, and uses thereof
An anisotropic, light-diffusing film technology, applied in the direction of nonlinear optics, optics, optical components, etc., to achieve the effects of maintaining illumination, high illumination, energy saving and sufficient sensitivity
- Summary
- Abstract
- Description
- Claims
- Application Information
AI Technical Summary
Problems solved by technology
Method used
Image
Examples
preparation example Construction
[0146] The method for producing the above-mentioned anisotropic light-diffusing laminate is not particularly limited. The method of bonding an anisotropic light-diffusion film and a plastic sheet together is mentioned.
[0147] An example of the bonding method using an adhesive (Japanese: Adhesive) or an adhesive (Japanese: Adhesive) will be described. Specific examples of the adhesives include rubber-based adhesives, acrylic adhesives, silicone-based adhesives, vinyl-based adhesives, and the like. Since the light reflector of the present invention may be used at high temperature, an adhesive stable even at normal temperature to 120°C is preferable. Among them, acrylic adhesives are widely used because they are inexpensive. Regardless of the adhesive used, its thickness is preferably 0.5 to 50 μm.
[0148] The above-mentioned adhesive is an adhesive that is bonded with the assistance of heat or a catalyst. Specifically, silicone-based adhesives, polyurethane-based adhesives, p
Embodiment 1
[0244] In a 60 mmφ single-screw extruder (L / D; 22), 47 parts by mass of ethylene-butene copolymer (manufactured by Mitsui Chemicals, Tuffma-A1085S) was mixed with polypropylene resin (manufactured by Sumitomo Chemical Co., Ltd., Sumitomo Noichi) Buren FS2011DG3) was melt-mixed at a resin temperature of 240°C in 53 parts by mass, extruded through a T-die, and then cooled with a casting roll at 20°C to obtain an unstretched sheet. Next, the unstretched sheet was stretched to 4.5 times at a stretching temperature of 118° C. using the difference in peripheral speed of the rollers of the longitudinal stretching machine, and then corona-treated on one side to obtain an anisotropic light-diffusing film with a thickness of 200 μm. The anisotropic light-diffusing film is formed of a structure including a continuous phase and a dispersed phase, and does not substantially contain voids. The anisotropic light-diffusing film obtained in this example was excellent in transmittance, diffusivi
Embodiment 2
[0248] 95 parts by mass of a substantially lubricant-free polyethylene terephthalate resin obtained by drying at 180° C. for 3 hours in a vacuum dryer to sufficiently remove moisture, and a low-density polyethylene resin manufactured by Prime Polymer Co., Ltd. ( SP1540) 5 parts by mass of the mixture is supplied to a single-screw extruder, melted at 280°C, and passed through a filter and a gear pump to remove foreign matter and equalize the extrusion amount, and then extrude in a sheet form through a T-die to The temperature was controlled to 25°C on a cooling cylinder. At this time, static electricity was applied using a wire-shaped electrode with a diameter of 0.1 mm, so that the sheet-shaped object was adhered to the cooling cylinder, and an unstretched film was obtained. Next, it stretched 3.0 times in the longitudinal direction at the temperature of 103 degreeC, and obtained the anisotropic light-diffusion film of thickness 75 micrometers. The anisotropic light-diffusing fi
PUM
Property | Measurement | Unit |
---|---|---|
Thickness | aaaaa | aaaaa |
Thickness | aaaaa | aaaaa |
Thickness | aaaaa | aaaaa |
Abstract
Description
Claims
Application Information
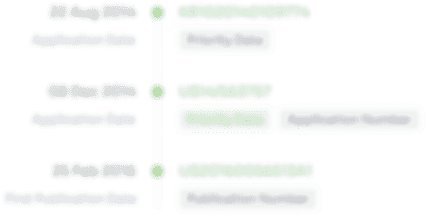
- R&D Engineer
- R&D Manager
- IP Professional
- Industry Leading Data Capabilities
- Powerful AI technology
- Patent DNA Extraction
Browse by: Latest US Patents, China's latest patents, Technical Efficacy Thesaurus, Application Domain, Technology Topic.
© 2024 PatSnap. All rights reserved.Legal|Privacy policy|Modern Slavery Act Transparency Statement|Sitemap