Method for controlling non-radial displacement transducer of multi-phase and single-winding bearingless motor
A bearingless motor and radial displacement technology, which is applied in motor generator control, electronically commutated motor control, electronic commutator, etc., can solve problems such as detecting rotor radial displacement, and reduce system cost and reduce system cost. Volume, cost reduction effect
- Summary
- Abstract
- Description
- Claims
- Application Information
AI Technical Summary
Benefits of technology
Problems solved by technology
Method used
Image
Examples
Embodiment Construction
[0023] The present invention is further described below in conjunction with the accompanying drawings:
[0024] like figure 1 As shown, the control method of the multi-phase single-winding bearingless motor without radial displacement sensor is:
[0025] Detect the current of each phase of the motor and the line voltage of the adjacent phase, and convert them to the following orthogonal d q plane coordinate systems of the motor through the multi-phase coordinate transformation link,
[0026]
[0027] in the formula represents the coordinate transformation matrix, is the rotor position angle, , when n is odd, the transformation matrix should delete the last row;
[0028] Select the d3-q3 plane which is different from the torque plane and the suspension plane in the multi-phase single-winding bearingless motor as the signal plane, keep the current of this plane at 0 through the current closed loop, and use the current feedback signal of the d2-q2 plane and the d3- After
PUM
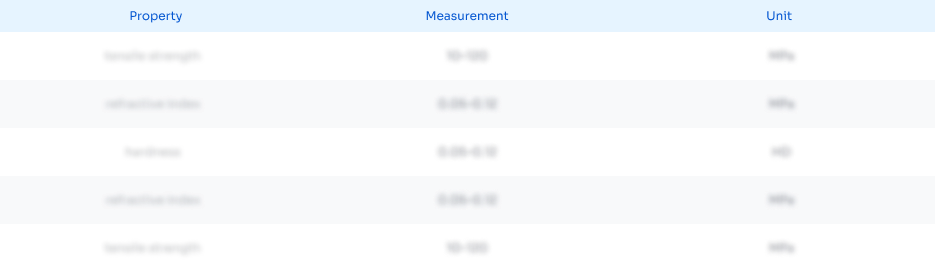
Abstract
Description
Claims
Application Information
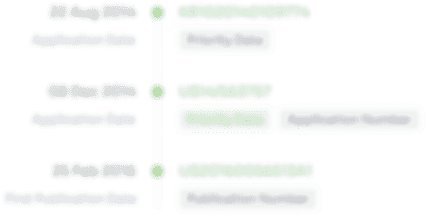
- R&D Engineer
- R&D Manager
- IP Professional
- Industry Leading Data Capabilities
- Powerful AI technology
- Patent DNA Extraction
Browse by: Latest US Patents, China's latest patents, Technical Efficacy Thesaurus, Application Domain, Technology Topic.
© 2024 PatSnap. All rights reserved.Legal|Privacy policy|Modern Slavery Act Transparency Statement|Sitemap