Water-cooling heat dissipation substrate
A water-cooled heat dissipation and substrate technology, used in electrical components, electrical solid devices, circuits, etc., can solve the problems of large volume, poor heat dissipation performance, complex structure, etc., and achieve the effect of small size, good cooling performance, and high integration.
- Summary
- Abstract
- Description
- Claims
- Application Information
AI Technical Summary
Benefits of technology
Problems solved by technology
Method used
Image
Examples
Embodiment Construction
[0015] refer to figure 1 with figure 2 , figure 1 The front view of the water-cooled heat dissipation substrate provided by the embodiment of the present invention; figure 2 for figure 1 The top view of the water-cooled heat sink substrate shown.
[0016] Such as figure 1 with 2 As shown, the water-cooled heat dissipation substrate provided in this embodiment includes a main board 1 , a water inlet connector 2 and a water outlet connector 3 . The water inlet joint 2 and the water outlet joint 3 are installed on the main board 1 and communicate with the coolant channel (not shown in the figure) inside the main board 1, specifically, the water inlet joint 2 and the water outlet joint 3 are connected to the main board through threaded holes and sealant. 1 The internal coolant channel is connected.
[0017] The main board 1 has a plurality of installation holes 11 for installing power devices of the converter.
[0018] Specifically, the main board 1 is a rectangular plate s
PUM
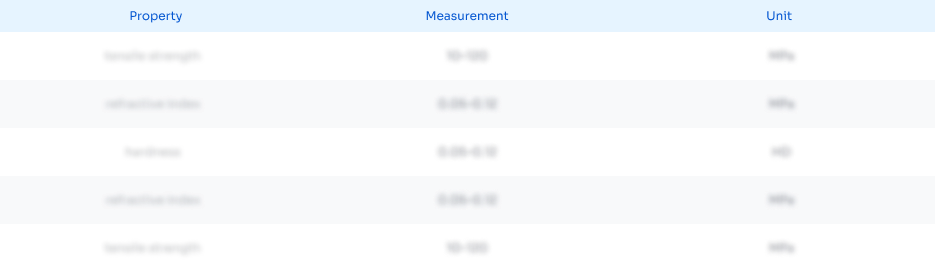
Abstract
Description
Claims
Application Information
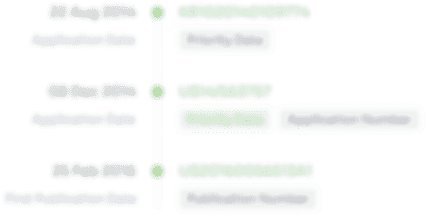
- R&D Engineer
- R&D Manager
- IP Professional
- Industry Leading Data Capabilities
- Powerful AI technology
- Patent DNA Extraction
Browse by: Latest US Patents, China's latest patents, Technical Efficacy Thesaurus, Application Domain, Technology Topic.
© 2024 PatSnap. All rights reserved.Legal|Privacy policy|Modern Slavery Act Transparency Statement|Sitemap