Measuring head space posture measuring method guided by ultrasonic positioning
An ultrasonic positioning and measurement method technology, applied in positioning, measuring devices, radio wave measuring systems, etc., can solve the problems of yaw error, measurement error, and inability to maintain parallel positions all the time, so as to improve accuracy and reliability, eliminate The effect of measurement error
- Summary
- Abstract
- Description
- Claims
- Application Information
AI Technical Summary
Problems solved by technology
Method used
Image
Examples
Embodiment Construction
[0010] Such as figure 1 , 2 As shown, a probe spatial attitude measurement method guided by ultrasonic positioning includes an ultrasonic positioning and guiding probe 1, and the ultrasonic positioning and guiding probe 1 includes a flat plate 2, and a group of Ultrasonic emission sensors 3, each group of ultrasonic emission sensors 3 has four ultrasonic emission sensors, the bottom edge of the flat panel 2 is connected with a probe 4, and the top edge of the flat panel 2 is equipped with an electromagnetic emission antenna 5, and each group of four ultrasonic emission sensors The sensor 3 is excited by four ultrasonic frequencies with different values. The normal direction of the vibration surface of each group of four ultrasonic transmitting sensors 3 points to the same direction on the outer surface of the plate where it is located. The ultrasonic positioning guides the four ultrasonic transmitting sensors 3 on one side of the probe 1. The ultrasonic signals of 4 different fr
PUM
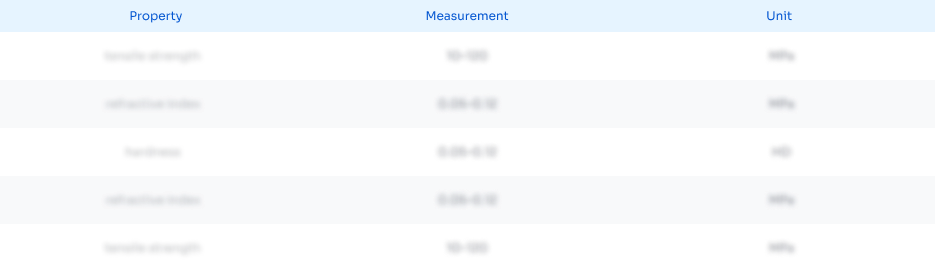
Abstract
Description
Claims
Application Information
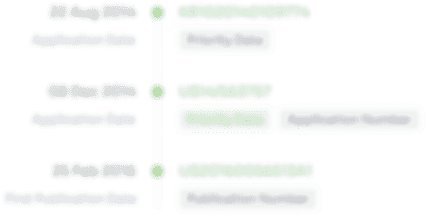
- R&D Engineer
- R&D Manager
- IP Professional
- Industry Leading Data Capabilities
- Powerful AI technology
- Patent DNA Extraction
Browse by: Latest US Patents, China's latest patents, Technical Efficacy Thesaurus, Application Domain, Technology Topic.
© 2024 PatSnap. All rights reserved.Legal|Privacy policy|Modern Slavery Act Transparency Statement|Sitemap