A Forced Six Degrees of Freedom Motion Apparatus
A technology of kinematic instrument and degree of freedom, which is applied in the direction of instruments, fluid dynamics test, machine/structural component test, etc. It can solve the problems of lack of frequency correlation, etc., and achieve increased contact strength and motion stability, compact structure, The effect of easy operation
- Summary
- Abstract
- Description
- Claims
- Application Information
AI Technical Summary
Problems solved by technology
Method used
Image
Examples
Embodiment Construction
[0019] The present invention will be further described below in conjunction with accompanying drawing example:
[0020] as attached figure 1 Shown, is the general arrangement drawing of the present invention; As attached figure 2 Shown is the front view of the experimental frame of the present invention; a forced six-degree-of-freedom motion instrument, including the experimental frame 1, the first pitch and roll connecting plate 3, the second pitch and roll connecting plate 4, the third horizontal and vertical It is composed of the rocking connecting plate 5, the fourth rolling and pitching connecting plate 6, the longitudinal torque servo motor driving device 2, the lateral torque servo motor driving device 7 and the gyrodynamic instrument 8. This device can perform seakeeping performance in the motion state of a six-degree-of-freedom ship model. Experiments are pitching, rolling, heave, yaw, surge and sway. Use the torque servo motor drive device to drive the pan and tilt c
PUM
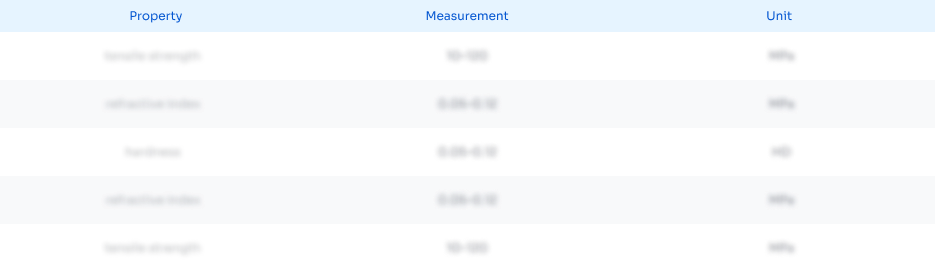
Abstract
Description
Claims
Application Information
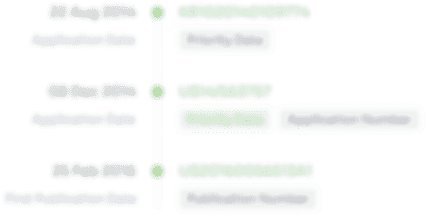
- R&D Engineer
- R&D Manager
- IP Professional
- Industry Leading Data Capabilities
- Powerful AI technology
- Patent DNA Extraction
Browse by: Latest US Patents, China's latest patents, Technical Efficacy Thesaurus, Application Domain, Technology Topic.
© 2024 PatSnap. All rights reserved.Legal|Privacy policy|Modern Slavery Act Transparency Statement|Sitemap