Paddy fieldwork vehicle frame assembly with lifting and rotating functions
A technology of rotating function and working vehicle, applied in the direction of lifting and manipulating vehicle accessories, vehicle maintenance, vehicle parts, etc., can solve the problems of increasing labor intensity and cost, crushing field stems, unable to turn U-turn, etc., to achieve convenient turning and U-turn , the effect of reducing labor intensity and reducing operating costs
- Summary
- Abstract
- Description
- Claims
- Application Information
AI Technical Summary
Problems solved by technology
Method used
Examples
Example Embodiment
[0028] Specific implementation manner one: such as Figure 1~Figure 10 As shown, the frame assembly of a paddy field operation vehicle with lifting and rotating functions includes a main frame 6, a front wheel 4, a rear wheel 5, a front hydraulic lifting pillar 29 and a rear hydraulic lifting pillar 30, front wheels 4, and rear wheels 5. The number of front hydraulic lifting pillars 29 and rear hydraulic lifting pillars 30 are two respectively. The main frame 6 is a horizontally arranged rectangular frame, and the two corners of the front end of the main frame 6 are each fixedly connected to a front hydraulic lifting pillar 29. , The two corners of the rear end of the main frame 6 are each fixedly connected to a rear hydraulic lifting column 30, the lower end of the front hydraulic lifting column 29 is fixedly connected to the front wheel 4, and the lower end of the rear hydraulic lifting column 30 is fixedly connected to the rear wheel 5. The paddy field work vehicle frame assembl
Example Embodiment
[0029] Specific implementation manner two: such as Figure 1 to Figure 3 , Figure 5 and Image 6 As shown, in the specific embodiment 1, the paddy field work vehicle frame assembly with lifting and rotating functions, the front hydraulic lifting strut 29 includes a front wheel strut 1, a front telescopic cylinder 2, a front wheel strut telescopic joint 3 and a front pin The number of the shaft 34 and the front pin shaft 34 is two. The front wheel pillar 1 and the front wheel pillar telescopic section 3 are both square tubes. The upper end of the front wheel pillar telescopic section 3 is arranged in the front wheel pillar 1, and the front wheel pillar telescopic section 3 is connected to the front wheel strut 1 in a sliding manner. The front telescopic cylinder 2 is arranged inside or outside the front wheel strut telescopic section 3. The cylinder body of the front telescopic cylinder 2 is connected to the front wheel strut 1 through a front pin 34. The telescopic rod is connecte
Example Embodiment
[0031] Specific implementation manner three: such as figure 1 , Figure 4 , Figure 8 to Figure 10 As shown, in the second embodiment of the paddy field work vehicle frame assembly with lifting and rotating functions, the middle hydraulic lifting pillar 31 includes a middle wheel pillar 8, a middle telescopic cylinder 23, a middle wheel pillar telescopic joint 9 and a middle pin The number of shaft 37 and middle pin shaft 37 is two. Both the middle wheel pillar 8 and the middle wheel pillar telescopic section 9 are square tubes. The upper end of the middle wheel pillar telescopic section 9 is set in the middle wheel pillar 8, and the middle wheel pillar telescopic section 9 is slidably connected to the middle wheel pillar 8, the cylinder body of the middle telescopic cylinder 23 is connected to the middle wheel pillar 8 through a middle pin shaft 37, and the telescopic rod of the middle telescopic cylinder 23 is connected to the middle wheel pillar telescopic section through the re
PUM
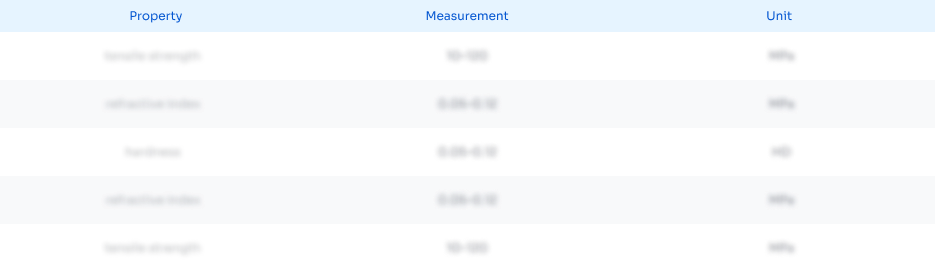
Abstract
Description
Claims
Application Information
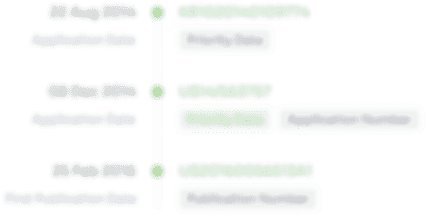
- R&D Engineer
- R&D Manager
- IP Professional
- Industry Leading Data Capabilities
- Powerful AI technology
- Patent DNA Extraction
Browse by: Latest US Patents, China's latest patents, Technical Efficacy Thesaurus, Application Domain, Technology Topic.
© 2024 PatSnap. All rights reserved.Legal|Privacy policy|Modern Slavery Act Transparency Statement|Sitemap