Molten iron jar melting agent and preparation method and application thereof
A technology of canned iron and molten iron, which is applied in the field of canned iron and its preparation, and can solve problems such as losses, rising pig iron costs, and falling off of refractory materials
- Summary
- Abstract
- Description
- Claims
- Application Information
AI Technical Summary
Benefits of technology
Problems solved by technology
Method used
Examples
preparation example Construction
[0013] The preparation method of described iron ladle canned iron agent, comprises pretreatment, preparation step, specifically comprises:
[0014] A. Pre-treatment: prepare materials according to the formula of ferric agent in molten iron tanks, pulverize anthracite and long-flame coal for later use, and purchase industrial salt and aluminum powder for later use;
[0015] B. Preparation: weigh the pulverized anthracite, long-flame coal, industrial salt and aluminum powder according to the formula ratio, mix and stir evenly to obtain the target product.
[0016] The particle size of the anthracite and long-flame coal is 1 mm to 3 mm, accounting for more than 90%.
[0017] The ladle canned iron agent is added into the iron can before putting iron in the blast furnace, adding 200kg to 500kg each time.
[0018] The inventive method, main definition, principle are as follows:
[0019] 1) Definition of ferric oxide
[0020] After adding the iron agent in the molten iron tank, a vio
Embodiment 1
[0027] Grind long-flame coal and anthracite for later use; purchase industrial salt and aluminum powder for later use; weigh 50 kg of long-flame coal, 20 kg of anthracite, 25 kg of industrial salt, and 5 kg of aluminum powder, and add them into a mixer to mix well to obtain Target.
Embodiment 2
[0029] The anthracite is crushed for later use; the industrial salt and aluminum powder are purchased for later use; 50kg of anthracite, 35kg of industrial salt, and 15kg of aluminum powder are weighed proportionally, added to a mixer and mixed to obtain the target product.
PUM
Property | Measurement | Unit |
---|---|---|
Granularity | aaaaa | aaaaa |
Abstract
Description
Claims
Application Information
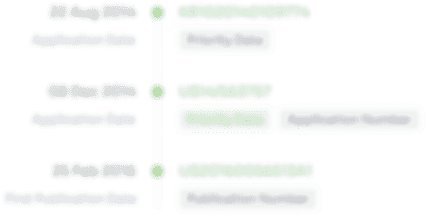
- R&D Engineer
- R&D Manager
- IP Professional
- Industry Leading Data Capabilities
- Powerful AI technology
- Patent DNA Extraction
Browse by: Latest US Patents, China's latest patents, Technical Efficacy Thesaurus, Application Domain, Technology Topic.
© 2024 PatSnap. All rights reserved.Legal|Privacy policy|Modern Slavery Act Transparency Statement|Sitemap